Wstęp
Prąd drożeje, trzeba oszczędzać ….
Jak? Obserwować, analizować, mierzyć, analizować, optymalizować.
Jedną z funkcjonalności systemu jest pomiar zużycia energii podłączonych maszyn i urządzeń.
Ale nie to jest najistotniejsze, tylko to że możemy się dowiedzieć ile prądu skonsumowała maszyna w konkretnym stanie.
Nie konkretnym czasie, to też, ale w konkretnym stanie: podczas produkcji, podczas przezbrajania, podczas postoju,
w trakcie realizacji konkretnego zlecenia produkcyjnego.
Sposób pomiaru
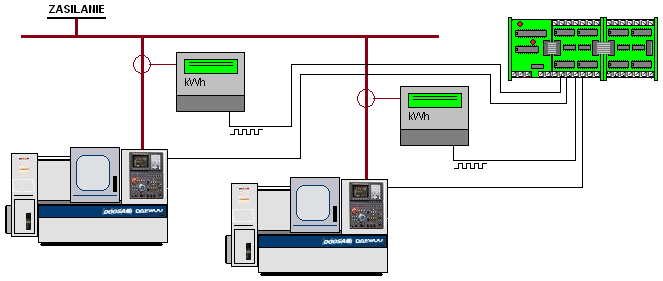
Idea pomiaru energii jest prosta: skoro system potrafi liczyć i przeliczać impulsy, np. impulsy z pakowarki na ilość pakietów to dla czego by nie przeliczyć impulsów z licznika energii elektrycznej który często wyposażony jest w wyjście impulsowe i nie przeliczyć na kWh ?
Pomiaru dokonuje odpowiednio skonfigurowany asystent. Sygnał z licznika podajemy na wejście ustalone w asystencie, określamy przelicznik który mówi jaka część kilowatogodziny jest reprezentowana przez jeden impuls oraz dla jakiej maszyny (nadzorcy) asystent ma liczyć energię.
Dobór liczników opisano w dokumancie:
Przykłady podłączenia maszyn - mini poradnik
na stronie 6
OEE a zużycie energi
Czy wartość wskaźnika OEE można przełożyć na zużycie energii? Bezpośrednio nie ale można założyć że w wielu sytuacjach spadek OEE może powodować straty energii. Szczególnie spadek wykorzystania może oznaczać zwiększone zużycie energii bo spadek wykorzystania oznacza że w tym samym czasie można było wykonać więcej, a więc szybciej skończyć zlecenie.
A krótsza praca to mniej prądu.
Podobnie jest ze stratą dostępności. Mogło by się wydawać że jak maszyna ma awarię to nie pracuje i nie pobiera energii.
Ale to nie zawsze prawda. Można sobie wyobrazić maszynę z pompą hydrauliczną z silnikiem powiedzmy 7 kW i awarię
podczas której operator czekał 30 minut na pomoc ale pompy nie wyłączył. Zakładając że pompa pobiera 1/3 mocy na ruchu jałowym to te pół godziny bezproduktywnego postoju kosztuje nas
2 kWh !
Również jakość ma wpływ na zużycie energii – zły produkt to zmarnowany prąd na jego wyprodukowanie.
Choć nie ma prostego przełożenia to możemy założyć że dążenie do poprawy wskaźników wydajnościowych takich jak OEE da nam dodatkową premię w postaci oszczędności energii.
Podział w/g statusu
Wartością w systemie nie jest sam pomiar energii. Wartością jest pomiar energii w funkcji aktualnego statusu.
Poza licznikiem „głównym” mamy liczniki które zliczają energię gdy:
- Ustawiony jest status PRACA
- Ustawiony jest status PRACA i biegnie czas pracy lub mikro postojów (maszyna rzeczywiście pracuje)
- Ustawiony jest status postój planowany lub konserwacja
- Ustawiony jest status awaria
- Ustawiony jest status postój nieplanowany
- Ustawiony jest status przezbrajanie lub ustawianie
Ekran obok pokazuje między innymi wykresy statusu dla aktualnego zlecenia, w tym wykres rozkładu energii.
Widzimy że od początku zlecenia maszyna skonsumowała 327 kWh w tym:
- Podczas statusu praca 345 kWh
- Podczas statusu praca rzeczywiście pracując 294 kWh
- Podczas statusu awaria 17kWh
- Podczas przezbrajania i ustawiania 7 kWh
- Podczas postoju i konserwacji 2.6 kWh
Można łatwo skorelować zużycie energii z pracą maszyny.
Przyjrzyjmy się fragmentowi wykresu miesięcznej linii czasu gdzie jeden krok reprezentuje 1 godzinę:
Widzimy dwa zlecenia [1] i [5] dwa odcinki czasu gdy maszyna była w stanie postoju planowanego [2] i [4] oraz
krótki odcinek czasu gdy maszyna była w statusie awaria [3].
Możemy odczytać zużycie energii w każdej godzinie i skorelować to zużycie z pracą maszyny lub jeśli maszyna nie pracowała z odpowiednim statusem w danej chwili.
I tak np. widzimy że podczas awarii [3] maszyna była załączona a podczas postoju planowanego [2] maszyna była wyłączona i nie pobierała energii. Zwróćmy jednak szczególną uwagę na postój planowany miedzy zleceniami [4].
Przykład z życia wzięty
Na tym wykresie odtworzono sytuację o której opowiadał nam kiedyś jeden z klientów.
Pomiędzy zleceniami maszyna nie pracowała ponad 2 dni. Po prostu nie było dla niej pracy. Ale nie wyłączono jej z zasilania pozostawiając z załączonym grzaniem. A w ciągu tego czasu maszyna skonsumowała niepotrzebnie ponad 1200 kWh.
To oczywiście przykład dość ekstremalny. Najczęściej tracimy na „drobiazgach”: tu 2kWh, tam 4kWh…
Ile zbiera się miesięcznie?
Raporty
Wykres rozkładu zużycia energii dostępny jest w raporcie zbiorczym dla maszyny i raporcie dla zlecenia produkcyjnego.
Wartość energii jest dostępna też w wielu innych raportach: miesięcznym, dziennym, grupowym, w kreatorze eksportów.
kWh/kg
Taka maszyna jak wtryskarka ( szerzej, maszyna przetwarzająca tworzywa ) może mieć różny poziom zużycia energii
zależnie od wielkości formy, wielkości wypraski, skuteczności chłodzenia itp. itd. Trudno więc porównać zużycie energii w stosunku do mocy zainstalowanej. Dwa różne produkty mogą znacząco różnić się energochłonnością
Dlatego branża stosuje wskaźnik określający ile energii potrzeba na przetworzenie jednego kilograma tworzywa, co zresztą definiuje norma Euromap 60.
System może szacować zużycie materiału - gramatura wyrobu z definicji zlecenia produkcyjnego x ilość wyprodukowana.
Mając do dyspozycji zużycie materiału i energii z łatwością wyliczymy parametr wyrażony w kWh/kg który określa faktyczną sprawność energetyczną procesu wtrysku.
Dodatkowo wprowadziliśmy też parametr określający ilość energii zużytej na wykonanie 1000 sztuk produktu co może być przydatne przy kalkulacjach.
Asystent zasilania
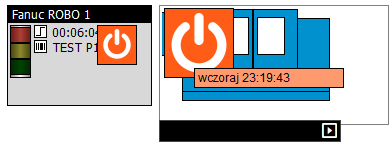
Możemy wykorzystać wejście koncentratora i podłączyć sygnał który mówi że maszyna ma zasilanie oraz stworzyć asystenta zasilania który będzie skojarzony z nadzorcą tej maszyny.
Asystent zasilania daje nam trzy korzyści:
- Pojawi się ikona zasilania gdy maszyna jest wyłączona
- W rejestrze zdarzeń on/off widoczne są informacje kiedy włączano / wyłączano maszynę
- Dostępny jest licznik godzin bez zasilania – możemy dla dowolnego okresu sprawdzić ile godzin w tym czasie maszyna była wyłączona
Jeśli zasilanie jest wyłączone a maszyna ma inny status niż postój planowany to ikona zasilania pulsuje.
Infrastruktura
Poza obserwacją pracy maszyn system pozwala na obserwację różnego rodzaju urządzeń takich jak sprężarki, chillery,
klimatyzatory itp. Urządzeń które często tworzą tło naszej produkcji pozostają niezauważonymi konsumentami sporej ilości energii.
Specjalny, uproszczony tryb agregatu z prostym sterowaniem statusu za pomocą wejść i uproszczona wizualizacją pozwala na obserwację prostych urządzeń. Tak jak w trybie maszyny tak i w trybie aparatu można do nadzorcy przypisać asystenta liczącego energię elektryczną.
Poniżej kilka przykładów:
Chiller
Przykładem monitorowania urządzeń infrastruktury może być nadzór nad agregatami chłodzącymi. W wielu branżach woda chłodząca jest sporym kosztem a wiec warto wiedzieć ile energii i kiedy zużywa agregat.
W przykładowym agregacie zastosowano sterowanie statusem dwoma wejściami: postój planowany, praca i awaria.
Główny sygnał monitoruje pracę sprężarki a asystent liczy zużytą energię.
Podobnie jak w przypadku maszyn mamy dostępny wykres miesięczny obrazujący status, ilość motogodzin, ilość załączeń agregatu oraz ilość zużytej energii w każdej godzinie.<
Oświetlenie hali
Aby kontrolować energię nie zawsze musimy ją mierzyć. Czasami wystarczy obserwować kiedy odbiorniki prądu są załączone.
Przykładem może być oświetlenie hali produkcyjnej czy magazynu. Na hali produkcyjnej czasami nigdy nie gasimy świateł, albo bardzo rzadko. Co innego magazyny – duża powierzchnia, duża ilość opraw a nie zawsze jest potrzeba aby światło paliło się tam 24 godziny na dobę.
Po podłączeniu oświetlenia do systemu możemy sprawdzić czy na przykład nocą, gdy nie ma produkcji, ochrona gasi światło o 22:30 jak się spodziewamy, o 1:10 jak im się przypomni czy może nie gasi wcale.
Licznik główny
Możemy stworzyć agregat który będzie monitorował baterię kondensatorów mocy biernej skonfigurowany w taki sposób
że licznik cykli będzie zliczał załączenia kompensacji a status sygnalizował awarię.
Do takiego agregatu dodamy asystenta energii który będzie współpracował z głównym licznikiem zakładu.
Możemy też dodać asystenta zdarzeń który będzie rejestrował alarmy „strażnika mocy” sygnalizujące przekroczenie limitu mocy.
Da nam to obraz zużycia energii przez cały zakład produkcyjny.