Okiem operatora
Prześledźmy obsługę systemu z punktu widzenia operatora maszyny.
Operator, nazwijmy go „Operator pierwszy” przychodzi do pracy i dostaje polecenie aby wykonać
4000 profili według zlecenia PCE113-3-MEST-11.
Maszyna, profilarka SMH1, jest w stanie postoju planowanego i ma zdemontowane oprzyrządowanie.
7:20
Operator „przejmuje” maszynę. Od tej pory Operator Pierwszy jest operatorem tej maszyny i jego nazwiskiem podpisane będą wszystkie zgromadzone dane.
7:23
Operator po wybraniu maszyny i zalogowaniu inicjuje nowe zlecenie – wybiera je z listy zleceń przygotowanej przez kolegów z planowania produkcji.
następnie zmienia status na: Przezbrajanie : Zmiana zespołu wykrojników i przystępuje do instalacji narzędzi.
Operator jeszcze dwukrotnie zmieni status, na Ustawianie: Załadunek blachy i na Ustawianie: Regulacja wykrojników podczas której ustawi prawidłową pracę maszyny
10:27
Po przygotowaniu maszyny do pracy i wykonaniu próbnych cykli operator zmienia status na
Praca:praca i rozpoczyna produkcję
11:43
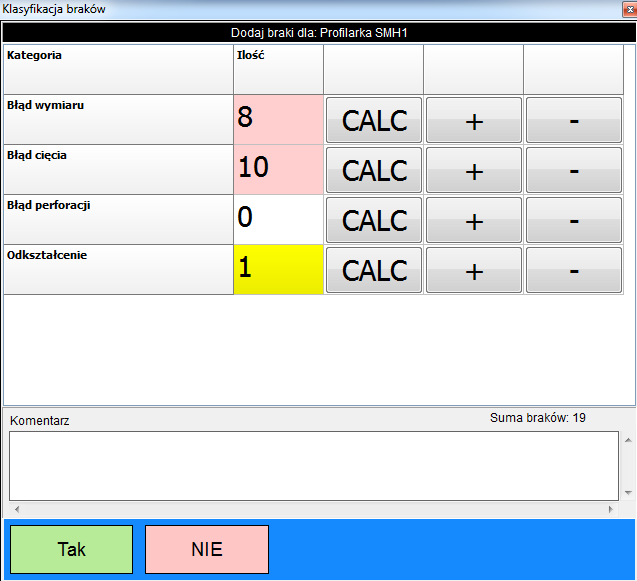
Operator wpisuje braki – wadliwe profile które zostały wykonane podczas rozruchu
oraz pierwszej partii produktu
12:07
Operator zauważa zatrzymanie maszyny spowodowane zaklinowanym stemplem.
12:32
po kilku próbach regulacji i inicjacji cyklu zmienia status na awarię i wzywa pomoc służb UR
12:44
Do maszyny dociera mechanik, Jan Kowalski i przejmuje maszynę do naprawy.
13:27
Mechanik Jan Kowalski po zakończeniu naprawy zmienia status na Praca:praca dodając krótką notatkę o wykonanej naprawie
14:23
Operator kończy pracę, zmienia status na Konserwacja: konserwacja po pracy
dodaje 14 braków
z kategorią „błąd perforacji” ( efekt niesprawnego stempla) i „zdaje maszynę” czyli przestaje być jej operatorem
Po godzinie 14 przyjdzie następny operator, przejmie maszynę, zmieni status na pracę i będzie kontynuował realizację zlecenia.
Awaria, wezwanie, naprawa
W systemie nie ma narzuconej zależności pomiędzy awarią ( statusem awaria ), naprawą czy wezwaniem pomocy Andon ale możemy przyjąć pewną procedurę, pewne założenia.
Kiedy jest awaria operator stwierdza że maszyna jest zepsuta i sam nic już nie poradzi, zmienia status na w awarię
i jednocześnie załącza wezwanie pomocy technicznej w systemie Andon.
Gdy pracownik UR przebędzie z pomocą pierwszą jego czynnością będzie odwołanie wezwania pomocy technicznej.
Gdy widzimy jednocześnie status awaria i wezwanie pomocy możemy domniemywać że jeszcze nikt z UR na awarię nie zareagował.
Pracownik UR może przejąć maszynę do naprawy przez co mówi wszystkim teraz JA naprawiam tę maszynę.
Dostępny jest raport dla UR który pokazuje w wybranym czasie ilość i czas awarii, ilość i czas wezwań pomocy technicznej i czas napraw, czyli czas przypisania do maszyny osoby naprawiającej
Premia za to że widać
Istnieje teoria że sam fakt wyraźnej widoczności problemu zmniejsza jego występowanie o 5%.
Dlatego prawie wszystkie maszyny mają świetlne kolumny sygnalizacyjne.
W systemie dostępne są aplikacje dedykowane do wyświetlania stanu maszyn na dużych monitorach.
Możemy wziąć duży telewizor z małym komputerkiem i powiesić nad maszyną jako uzupełnienie kolumny. Koszt 40 calowego telewizora z małym, przykręcanym z tyłu komputerkiem to raptem 4 krotność ceny porządnej kolumny świetlnej.
Na ekranie widać że maszyna jest w stanie awarii.
Widać że awaria trwa już 11 minut. Widać też że od 11 minut aktywne jest wezwanie pomocy
co może sugerować że awarią jeszcze nikt się nie zajął…
Podobny telewizor możemy powiesić w biurze szefa produkcji, w warsztacie UR, gabinecie prezesa, na stołówce.
Wszędzie widać ten sam problem…
Po przywróceniu maszyny do sprawności wyświetlany jest stan aktualnego zlecenia
Na wykresie reprezentującym status z ostatnich 24 godzin widzimy że awaria trwała około 2 godzin.
GEMBA Walking - Idż i zobacz
Każdy kto zajmuje się produkcją słyszał o jednej z technik lean manufacturing: GEMBA Walking czyli w skrócie i uproszczeniu: idź na produkcję i sam zobacz.
Czyli dobry menadżer powinien chodzić do miejsc pracy i obserwować procesy z bliska.
Jest jednak jeden drobny problem. Zgodnie z zasadą nieoznaczoności Heisenberga obserwator ma bezpośredni wpływ na obserwowany proces. Mówiąc po ludzku – jak pójdę na halę i będę patrzył to praca będzie wrzała dla tego że … patrzę.
System Golem daje możliwość ciągłego
dyskretnego nadzoru nad produkcją. W każdej chwili możemy „rzucić okiem” na stan obecny oraz na wydarzenia z ostatnich godzin a potem pójść na halę i dopytać o szczegóły co ma dwie zalety:
- Możemy na bieżąco analizować proces i wyłapywać jego zakłócenia
- Pracownicy wiedzą że możemy na bieżąco analizować proces i wyłapywać jego zakłócenia
Zestawienie dla grupy
Widok grupy pozwala przyjrzeć się grupie maszyn jako całości.
Pierwszy wykres pokazuje ile maszyn z grupy znajduje się obecnie w poszczególnych statusach: 3 maszyny mają postój planowany, 1 postój nieplanowany, 1 awarię a 5 jest w statusie praca z czego 4 faktycznie pracują a jedna nie.
Poniżej mamy wykres ostatnich 24 godzin który pokazuje uśredniony rozkład statusów z wszystkich maszyn.
Następnie mamy wykresy SUMARYCZNE statusów i OEE dla aktualnej i minionych zmian.
Zwróćmy uwagę że OEE jest wyznaczane dla wszystkich maszyn i oddzielnie z pominięciem tych maszyn które w badanym zakresie przez cały czas miały postój planowany.
Narzędzia do oceny całej grupy są bardzo kuszące – każdy chciałby ocenić całość jednym wskaźnikiem. Ale należy być ostrożnym w analizie takich danych bo to trochę tak jak smakowanie wody z wiadra do którego wlano kieliszek wódki …
Kilka zjawisk na osi czasu
Idż i dopytaj
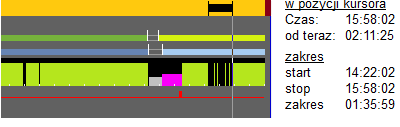
Analizując wykres czasu widzimy że około 2 godzin temu, pomiędzy 14:20 a 15:58, czyli przez ponad 1,5 godziny
maszyna miała przerwę w pracy. Nie była to pełna przerwa bo widać próby podjęcia pracy ale też nie zmieniono statusu na inny, np. na awarię.
Ponieważ minęły dopiero dwie godziny to możemy przejść się na halę i spróbować się dowiedzieć od pracowników co było powodem tego przestoju.
Przejść się teraz. Nie jutro czy pojutrze tylko TERAZ. Jutro nikt już nie będzie pamiętać co się wydarzyło a godzina czasu nieoznaczonego po prostu powiększy nam sumę strat.
Pracujecie? Pracujemy, pracujemy
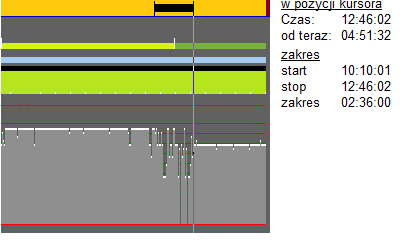
Jeśli spojrzymy na wykres, na pasek statusu to serce się raduje – maszyna pracuje bez żadnych przerw od ponad 18 godzin.
Jeśli jednak rozwiniemy wykres wydajności to się okazuje że tak kolorowo to nie jest. Do 10:10 maszyna pracowała w miarę płynnie z zakładaną wydajnością. Ale potem coś się stało. Pomiędzy 10:10 a 12:40 widać wyraźne zakłócenia w pracy maszyny skutkujące znacznymi spadkami wydajności a od godziny 12:46 maszyna pracuje płynnie ale z dużo niższą wydajnością niż poprzednio
przy czym nic na wykresie nie sugeruje aby dokonano zmiany produktu..
Ile naprawdę trwa awaria?
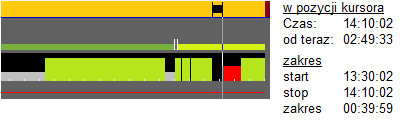
Niecałe 2 godziny temu, o 14:10 była awaria (zmieniono status na awarię ) która trwała około 70 minut. Ale…
Awarię poprzedza ok 40 minut „nie pracy”.
Co to może oznaczać? Może oznaczać że maszyna zatrzymała się około 13:30 i do 14:10 nikt tego nie zauważył. Technik utrzymania ruchu został wezwany zapewne dopiero po godzinie 14:10. Z punktu widzenia utrzymania ruchu awaria trwała
70 minut ale maszyna była zepsuta ponad 110 minut.
Dlatego Golem jest silnym narzędziem dla UR ponieważ można dość precyzyjnie określić jaka część awaryjnego postoju maszyny obniża nam jej dostępność co jest w gestii inżynierów i techników a jaka część zaniża wykorzystanie co jest w gestii szefostwa produkcji.
A kiedy już sobie wyjaśnimy co jest czyje to to jest szansa aby płynnie przejść ze spychologii na współpracę.
Powiadomienia e-mail
Informacje możemy dostać też w formie listów email. Jest to szczególnie pożyteczne narzędzie w przypadku gdy zakład produkcyjny jest w innej lokalizacji a z jakiegoś powodu nie mamy sieci prywatnej.
Raportowanie w formie listów elektronicznych mogą być zmiany statusu i przywołań andon albo wszystkie powiadominia.
Możemy też dostawać mikro raporty na koniec zmiany roboczej lub na koniec zlecenia.
przykładowe e-maile
Zmiana statusu
Tytuł:
wtryskarka A1 T0Z1 Zmiana statusu AWARIA : Awaria robota
Treść:
2018-10-01 13:06:19 wtryskarka A1 T0Z1
Zmiana statusu AWARIA : Awaria robota
USR: Operator Pierwszy
Comment:
robot gubi wypraski
Fragment raportu dla zmiany roboczej
Tytuł:
Podsumowanie zmiany roboczej
Treść:
2018-10-01 14:00:00
----------------------------------------------------
Prasa PZ1A
OEE: 0.00% D: 00.00% W: 00.00% J: 100.00%
Efektywny czas pracy: 00:00:00 [32.17%] Produkt:0 Braki:0
----------------------------------------------------
Prasa PZ2A
OEE: 80.18% D: 100.00% W: 80.18% J: 100.00%
Efektywny czas pracy: 03:34:39 [30.97%] Produkt:25 760 Braki:0
2018-10-01 10:25:21>> Wznowienie pracy po 08:21:12 przerwy OP: GOLEM MES
----------------------------------------------------
Prasa PZ3A
OEE: 99.81% D: 100.00% W: 99.81% J: 100.00%
Efektywny czas pracy: 00:26:44 [73.44%] Produkt:3 216 Braki:0
2018-10-01 13:22:10>> Operator przejmuje maszynę OP:Operator Pierwszy
2018-10-01 13:22:26>> Kasowanie liczników (quasi-zlecenie) OP:Operator Pierwszy
2018-10-01 13:23:06>> Zmiana statusu Ustawianie OP:Operator Pierwszy
2018-10-01 13:23:36>> Kasowanie liczników (quasi-zlecenie) OP:Operator Drugi
2018-10-01 13:23:42>> Operator przejmuje maszynę OP:Operator Drugi
2018-10-01 13:33:13>> Zmiana statusu PRACA OP:Operator Drugi
2018-10-01 13:33:16>> Wznowienie pracy po 15D 22:44:47 przerwy OP: GOLEM MES
----------------------------------------------------
Prasa PP1
OEE: 0.00% D: 100.00% W: 00.00% J: 100.00%
Efektywny czas pracy: 00:00:00 [0.63%] Produkt:0 Braki:0
2018-10-01 13:21:06>> Zmiana statusu Ustawianie OP:Operator Pierwszy
koniec zlecenia
Tytuł:
Koniec zlecenia PCE3416-24XTEM2
Treść:
2018-10-01 12:33:22
Profilarka SMH1
zlecenie: PCE3416-24XTEM2
produkt: PROFIL CE113-200X85X30
OEE: 64.65% D: 69.78% W: 93.53% J: 99.05%
Efektywny czas pracy: 01:13:45 [57.23%] Produkt: 2 527 Braki: 24
2018-10-01 10:24:30>> Nowe zlecenie OP:Neuron Soft
2018-10-01 10:24:41>> Zmiana statusu USTAWIANIE : Załadunek blachy OP:Neuron Soft
2018-10-01 10:24:51>> Operator przejmuje maszynę OP:Operator Pierwszy
2018-10-01 10:40:22>> Zmiana statusu PRACA : Praca OP:Operator Pierwszy
2018-10-01 10:40:53>> Wznowienie pracy po 13:20:13 przerwy OP: GOLEM MES
2018-10-01 10:58:26>> Zmiana statusu POSTóJ NIEPLANOWANY : Brak palet odbiorczych OP:Operator Pierwszy
2018-10-01 11:13:12>> Zmiana statusu PRACA : Praca OP:Operator Pierwszy [ część palet jest w złym stanie ]
2018-10-01 11:13:13>> Wznowienie pracy po 00:14:47 przerwy OP: GOLEM MES
2018-10-01 11:54:55>> Zmiana statusu AWARIA : Awaria maszyny OP:Operator Pierwszy [ Nie można załączyć maszyny ]
2018-10-01 12:14:18>> Zmiana statusu PRACA : Praca OP:Operator Pierwszy
2018-10-01 12:14:35>> Wznowienie pracy po 00:20:44 przerwy OP: GOLEM MES
2018-10-01 12:27:55>> Osiągnięto 95% ilości zamówionej OP: GOLEM MES
2018-10-01 12:32:18>> Osiągnieto ilość zmówioną OP: GOLEM MES
2018-10-01 12:33:22>> Koniec zlecenia OP:Operator Pierwszy
Produkcja nakrętek w/g zlecenia
Dużą zaletą systemu jest śledzenie nie tylko pracy maszyn ale i realizacji zleceń produkcyjnych.
Prześledźmy zatem przebieg jednego, przykładowego zlecenia na wykonanie 35 tysięcy nakrętek.
Narzędzie
Realizację zlecenia zaczynamy od dodania formy wtryskowej do kartoteki narzędzi

Dodając narzędzie podajemy oczywiście nazwę i oznaczenie, status czy opis. Dodajemy też zestaw parametrów dla zlecenia które będzie realizowane z użyciem tego narzędzia. Parametry te zostaną użyte podczas tworzenia produktu – gdy wybierzemy narzędzie podczas edycji produktu zostaną one przepisane do parametrów produktu.
Możemy więc powiedzieć że są to parametry domyślne.
Dodane narzędzie jest widoczne w kartotece.
Możemy teraz dodać jeszcze dwa zdjęcia i plik pdf z kartoteki plików pdf, np. procedurę instalacji SMED.
Produkt
Teraz dodamy produkt w kartotece produktów.
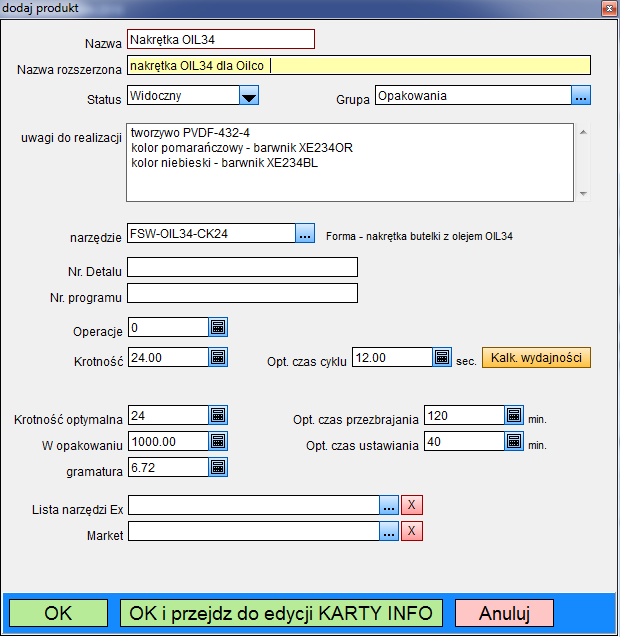
Ustalamy nazwę produktu która będzie widoczna w całym programie, nazwę rozszerzoną, uwagi do realizacji – te będą widoczne podczas wybierania produktu lub zlecenia.
Po wybraniu narzędzia zostaną przepisane parametry które oczywiście możemy dowolnie zmienić. Albo wpisać gdy nie wybieramy narzędzia bo
ważne jest to że w edytorze widoczne są wszystkie parametry nawet jeśli nie będą potrzebne bo np. czas cyklu ustalany jest w konfiguracji a nie w zleceniu.
Po dodaniu produktu do kartoteki możemy produkt powiązać z maszyną / maszynami.
Podczas wyboru produktu widzimy tylko te które są powiązane z odpowiednią maszyną oraz te które nie są powiązane z żadną.
Dla każdego produktu możemy zdefiniować kartę informacyjną produktu.
Operator w dowolnym momencie może wyświetlić tę kartę.
Poza parametrami realizacji produktu karta może zawierać dwa dowolne pola notatnikowe z opisami, 4 zdjęcia i dwa linki do plików pdf.
Jeśli produkt jest powiązany z narzędziem to dodana jest zakładka z opisem narzędzia i jego zdjęciami.
Menadzer zleceń
Teraz możemy przygotować zlecenie które wybierze operator maszyny.
Podczas tworzenia zlecenia wybieramy produkt co powoduje zaimportowanie wszystkich parametrów,
podajemy numer zlecenia i ilość zamówioną jeśli jest używana.
Kolejność zleceń (a właściwie kolejność ich wyświetlania) w ramach maszyny możemy zmienić manipulując wartością kolumny sort.
Dodane zlecenie może zostać oznaczone jako ukryte dla operatora – nie będzie ono widoczne w oknie wyboru zlecenia – możemy ukryć zlecenie jeśli chcemy je już teraz dodać ale odkryć do realizacji za kilka dni.
Jeśli zlecenie jest przekreślone to oznacza że zostało już użyte (wybrane do realizacji)
Realizacja zlecenia
10:38 Start zlecenia, przezbrajanie
Przygotowaliśmy zlecenie w menadżerze zleceń dla maszyny WTRA-2M. Gdyby realizowano je na tej maszynie to operator wybrał by jedynie zlecenie z listy.
My jednak uruchomimy realizacje zlecenia na wtryskarce A1 która jest skonfigurowana w taki sposób że to operator tworzy zlecenie wybierając produkt z listy produktów i dopisując nazwę zlecenia i ilość zamówioną.
W rejestrze powiadomień widzimy wpisy o nowym zleceniu i o rozpoczęciu przezbrajania.
W panelu info, na zakładce zlecenie mamy przycisk [Analiza] który otwiera nam okienko z wyliczeniami czasu potrzebnego do realizacji zlecenia.
12:52 Początek produkcji, odpad
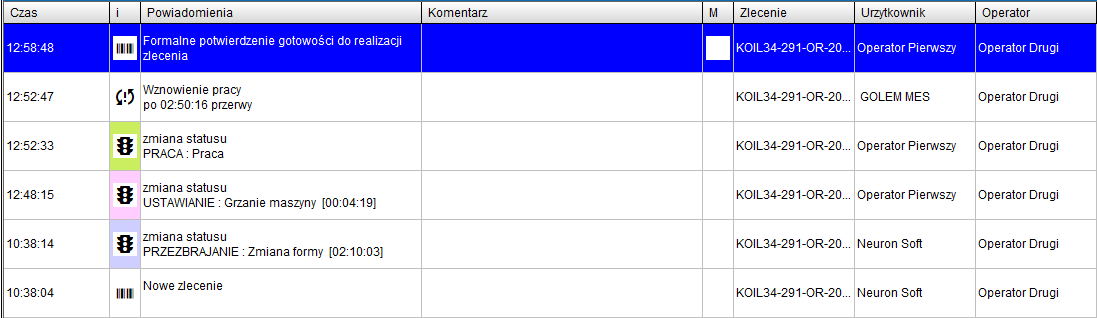
Z widocznych powiadomień wynika że:
- o 12:48 zakończono przezbrajanie maszyny (po 4 godzinach i 19 minutach) i rozpoczęto jej granie
- o 12:52 zmieniono status na pracę, maszyna ruszyła o 12:52
- o 12:58 operator potwierdził gotowość maszyny do realizacji zlecenia
Zwróćmy uwagę na czas przezbrajania:

Przezbrojenie trwało 2 godziny i 10 minut. W definicji zlecenia podano optymalny czas przezbrojenia równy dwie godziny.
Czyli przezbrojenie trwało o 10 minut dłużej niż przewiduje norma.
Dwie godziny z czasu przezbrojenia nie są stratą i zaniżają czas operacyjny. 10 minut czasu ponadnormatywnego zaniża dostępność maszyny.
Po rozpoczęciu produkcji operator odrzucił pierwszą partię produktu i wpisał do systemu jako odpad
14:00 Zmiana operatora
16:30 Stan produkcji
Rzut oka na stan produkcji
Na wykresie postępu zlecenia widzimy że wykonano 46% zamówionej ilości, że w ramach zlecenia zarejestrowano 120 braków, produkowane jest 17 opakowanie zbiorcze (do zrobienia jest 35 opakowań).
Zakończenie zlecenia (przy założeniu utrzymania bieżącego tempa) prognozowane jest na godzinę 18:11 ( za 2,5 godziny)
Mamy też przyzwoite wskaźniki dla zlecenia.
Dostępność zaniżona jedynie o 10 minut przezbrajania ponad normę, wykorzystanie na poziomie 84% ( ok 25 minut na krótkie zatrzymania czy straty wydajności), jakość w normie.
OEE 78% mówi nam że wykorzystaliśmy jak dotąd 78% możliwości.
17:45 Awaria formy, zmiana krotności
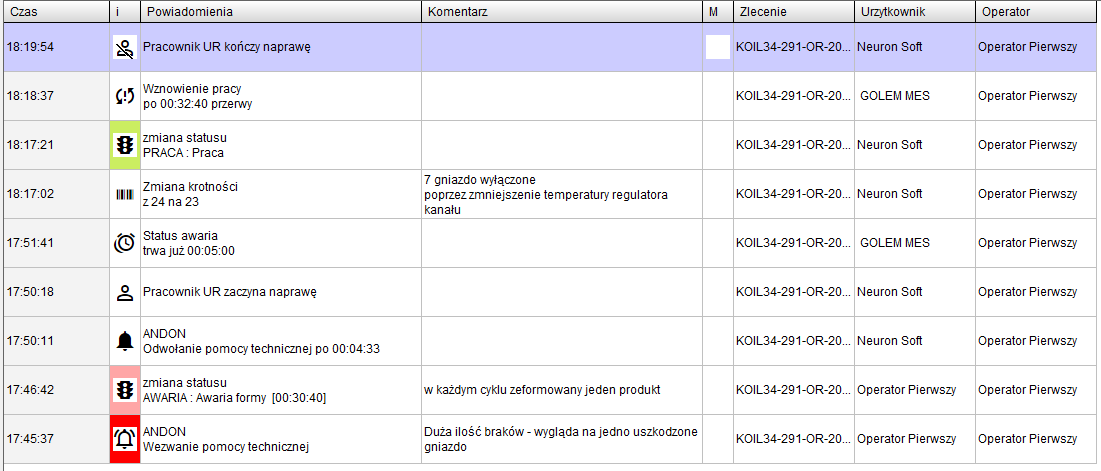
Z widocznych powiadomień wynika że:
- o 17:45 operator wzywa pomoc techniczną i zmienia status na awarię formy
- o kilka minut później pojawia się pracownik utrzymania ruchu, zaczyna naprawę i odwołuje wezwanie
- o 18:17 pracownik UR zmienia krotność z 24 na 23 – zablokowano uszkodzone gniazdo za pomocą regulatora kanału, następnie zmienia status na pracę, maszyna wznawia produkcję a pracownik UR kończy naprawę
18:55 Koniec zlecenia
Zlecenie zostało zakończone ze stratami wynikającymi z awarii (30minut) oraz z niewielkimi stratami wynikającymi z pracy z jednym niesprawnym gniazdem co pokazuje wskaźnik CAVITY. Stracono tylko pół procenta ale jeśli realizacja zlecenia trwała by dłużej albo była by to na przykład forma 4-gniazdowa która utraciła jedno gniazdo to straty były by znaczące.
Raport dla zlecenia
Raport przebiegu zlecenia
Narzędzia eksploatacyjne
W branży obróbki metali ( choć nie tylko ) sporym kosztem są narzędzia takie jak frezy, płytki tokarskie wiertła itp. itd.
Kontrolą ich stanu a także zużycia zajmują się programy do obsługi narzędziowni i system Golem nie ma zamiaru wchodzić w ich zakres kompetencji.
Programy takie jednak pozwalają na ogólne zużycie narzędzi – w tym miesiącu zużyto 24 frezy XYZ.
System Golem próbuje dostarczyć odpowiedzi na pytanie o kontekst tego zużycia: kiedy, na jakiej maszynie, podczas jakiego zlecenia produkcyjnego i dla czego.
Idea jest bardzo prosta – tworzymy bazę narzędzi, ale nie wszystkich, tylko tych drogich, narażonych na zniszczenie, albo masowo zużywanych a operator maszyny kiedy wymienia takie narzędzie z powodu zużycia albo zniszczenia informuje o tym system który fakt utylizacji narzędzia oznacza czasem, nazwą maszyny, nazwiskiem operatora oraz numerem zlecenia.
Rejestr i grupa narzędzi
Najpierw przygotowujemy bazę narzędzi eksploatacyjnych.
Dodajemy te wszystkie narzędzia nad którymi chcemy mieć kontrolę.
Następnie przygotowujemy grupy narzędzi. Po co?
Po to aby maksymalnie uprościć pracownikowi wyszukiwanie narzędzi. Grupa będzie dołączona do maszyny albo do produktu.
Jeśli maszyna większość czasu poświęca na zgrubną obróbkę produktu to może być tak że w praktyce używa 2-4 frezów które „zajeżdża” w dużych ilościach. Po przygotowaniu odpowiedniej grupy pracownik zobaczy tylko te 2-4 frezy
Kontrola w ramach zlecenia
Prześledźmy realizację zlecenia produkcyjnego realizowanego na maszynie do której przypisano powyższa grupę narzędzi.
O godzinie 15:45 operator zmuszony był wymienić frez. Fakt ten został zaraportowany za pomocą formularza „utylizacja narzędzia eksploatacyjnego”
Nim skończy się zlecenie operator jeszcze trzy razy zaraportuje wymianę narzędzia, raz z powodu jego zniszczenia podczas awarii.
Zerknijmy na powiadomienia związane z tym zleceniem.
Widzimy że w ciągu 5 godzin pracy 4 razy wymieniano narzędzia: 3 razy frez dwu ostrzowy i raz frez zgrubny.
Jeden z frezów wymieniono z powodu jego zniszczenia podczas awarii maszyny.
Przeglądanie rejestru powiadomień to najskuteczniejsza metoda analizy gdyż widzimy cały kontekst zdarzeń a dla każdego powiadomienia przypisana jest ilość produktów od początku zlecenia czy zmiany.
Jeśli wymiana narzędzia jest kosztowna czasowo to możemy zdefiniować na tę okoliczność status – tak jak w tym przykładzie. Będziemy mogli analizować nie tylko zużycie narzędzi ale też ilość czasu poświęcanego na ich wymianę.
Poza analizą powiadomień mamy do dyspozycji historię każdego wskazanego narzędzia w kartotece narzędzi eksploatacyjnych oraz jej rozwinięcie w formie większego narzędzia.
Możemy na przykład założyć filtr na wybrany produkt aby określić jaki jest jego koszt wyrażony w narzędziach
Przedstawiona powyżej metoda kontroli zużycia narzędzi daleka jest od ideału. Z drugiej strony ciężko sobie nawet wyobrazić idealne rozwiązanie – wymagało by ono otagowania tysięcy narzędzi, pozyskania danych z programu narzędziowni, pozyskania danych o automatycznej zmianie i pomiarach narzędzi itp. itd. itp. …
Jednak nawet takie proste rozwiązanie zmusi operatora który ma obowiązek raportować zużycie i który wie że te dane ktoś śledzi, nawet takie proste rozwiązanie zmusi operatora aby się pięć razy zastanowił zanim „podkręci obroty”