Korzyści, czyli miejmy ten temat z głowy
Wiele opracowań o systemach MES koncentruje się na korzyściach z ich stosowania często stosując taką narrację że zmierzenie problemów jest ekwiwalentne z ich eliminacją. Czasami nawet podają w procentach o ile to wzrośnie efektywność, spadną straty, poprawi się jakość, wystarczy wdrożyć system ….To tak nie działa…
System MES dostarcza informacje. O produktywności, postojach, brakach, a nader wszystko o mikro postojach. Wiedzę często dostępną szybko ( wskaźniki KPI, wizualizacja ) i kompleksowo ( systemy raportowania ). Wiedzę o dość dużym poziomie rzetelności, szczególnie dzięki korelacji informacji z rzeczywistą pracą maszyn.
Ale to od użytkowników systemu zależy czy, jak i jak szybko z tej wiedzy skorzystają.
Jednym te informacje pomogą w ciągłej optymalizacji produkcji, w ciągłym „urywaniu” tu i tam po kilka procent. Innym pokażą gdzie są dziury w systemie o których nie wiedzieli albo nie zdawali sobie sprawy z ich skali.
O jednej korzyści na pewno warto wspomnieć, o swego rodzaju efekcie psychologicznym. Świadomość u pracowników jak i menadżerów że możliwe jest dość dokładne odtworzenie tego co się działo daje nieraz zaskakujące efekty. Czasami możemy dostać kilka, kilkanaście procent premii za sam fakt wdrożenia systemu. Ale uwaga, tę premię łatwo roztrwonić.
Klasyczna definicja
Za Wikipedią:Systemy klasy MES wykorzystując technologie informatyczne, urządzenia i elementy automatyki, umożliwiają zbieranie informacji w czasie rzeczywistym wprost ze stanowisk produkcyjnych i ich transfer na obszar biznesowy.
Dzięki funkcjonalności systemu można uzyskać natychmiastowy sygnał zwrotny o stopniu wykonania produkcji, podejmować na bieżąco właściwe decyzje i reagować na bieżąco na nieprawidłowości pojawiające się w czasie procesu produkcyjnego.
11 obszarów funkcjonalnych systemów MES wg organizacji MESA International:
- harmonogramowanie produkcji (Scheduling)
- rozdział zadań produkcyjnych ( Dispatching Production Units)
- zarządzanie wykonywaniem produkcji (Process Management)
- gromadzenie i akwizycja danych (Data Collection and Aquisition)
- zarządzanie wydajnością (Performance Analysis)
- śledzenie produkcji i jej genealogia (Traceability)
- zarządzanie jakością (Quality Management)
- zarządzanie obiegiem dokumentów (Document Control)
- zarządzanie alokacją zasobów ( Resource Allocation)
- zarządzanie zasobami ludzkimi (Labor Management)
- zarządzanie ruchem (Maintenance Management)
MOM to w zasadzie termin marketingowy mający podkreślić że dostawca oferuje nie tylko system MES który jest podzbiorem funkcjonalności systemu MOM ale oferuje wszystkie narzędzia ( bądź integracje z nimi ) do kompleksowego zarządzania i optymalizowania procesu produkcyjnego.
Tyle teorii …
Kilka słów o systemach SCADA
Zanim przejdziemy do systemów MES musimy powiedzieć kilka słów o systemach SCADA( Supervisory Control And Data Acquisition).
SCADA to system informatyczny nadzorujący przebieg procesu technologicznego lub produkcyjnego. Jego główne funkcje obejmują zbieranie aktualnych danych (pomiarów), ich wizualizację, sterowanie procesem, alarmowanie oraz archiwizację danych. Głównie poprzez komunikację ze sterownikami PLC sterującymi maszynami i instalacjami produkcyjnymi oraz komunikację z wszelakiego rodzaju urządzeniami pomiarowymi.

Pierwsze systemy SCADA pojawiły się wraz z pierwszymi komputerami zbierając i przetwarzając głównie dane procesowe takie jak temperatury, ciśnienia, poziomy w zbiornikach itp.
W przemyśle chemicznym, w systemach wentylacyjnych, w przemyśle spożywczym czy energetyce, wszędzie tam gdzie każdy parametr, każda jego odchyłka mogła być krytyczna dla procesu.
Wraz z upowszechnianiem się systemów SCADA zaczęły one trafiać też do pojedynczych linii produkcyjnych, liczyć produkty, kontrolować czasy cykli itp.
Można więc powiedzieć że pierwsze systemy MES były systemami SCADA z odpowiednio zaprogramowanymi funkcjami i rozbudowaną integracją z innymi systemami.
MES w potoczny rozumieniu
Na rynku jest bardzo dużo rozwiązań. Są proste systemy chmurowe oparte na niezależnych czujnikach, np. Evocon czy Fitmech. Są rozwiązania sprzedawane dosłownie „z półki” takie jak nasz Golem OEE MES oparty na własnych modułach wejść binarnych.Są systemy dedykowane dla konkretnej branży jak ProSeS dla wtryskarek czy Cimco i Scout dla maszyn CNC.
Są też potężne platformy do tworzenia oprogramowania produkcyjnego takie jak Siemens Opcenter, Wonderware MES i wiele podobnych. Choć w przypadku platform trzeba pamiętać że często zmieniają one nazwy, zakresy funkcjonalności a nawet właścicieli.
No i są systemy ERP z modułami raportowymi które pretendują do miana systemów MES o czym niżej.
Pomimo potężnych możliwości niektórych systemów, (podobno Opera MES w kolaboracji z Asprowa APS może wszystko – jeśli mamy siły, środki i cierpliwość) to jednak większość ludzi postrzega system MES jako system monitorujący pracę maszyn lub trochę szerzej monitorujący wykonanie pracy (zleceń produkcyjnych) na tych maszynach.
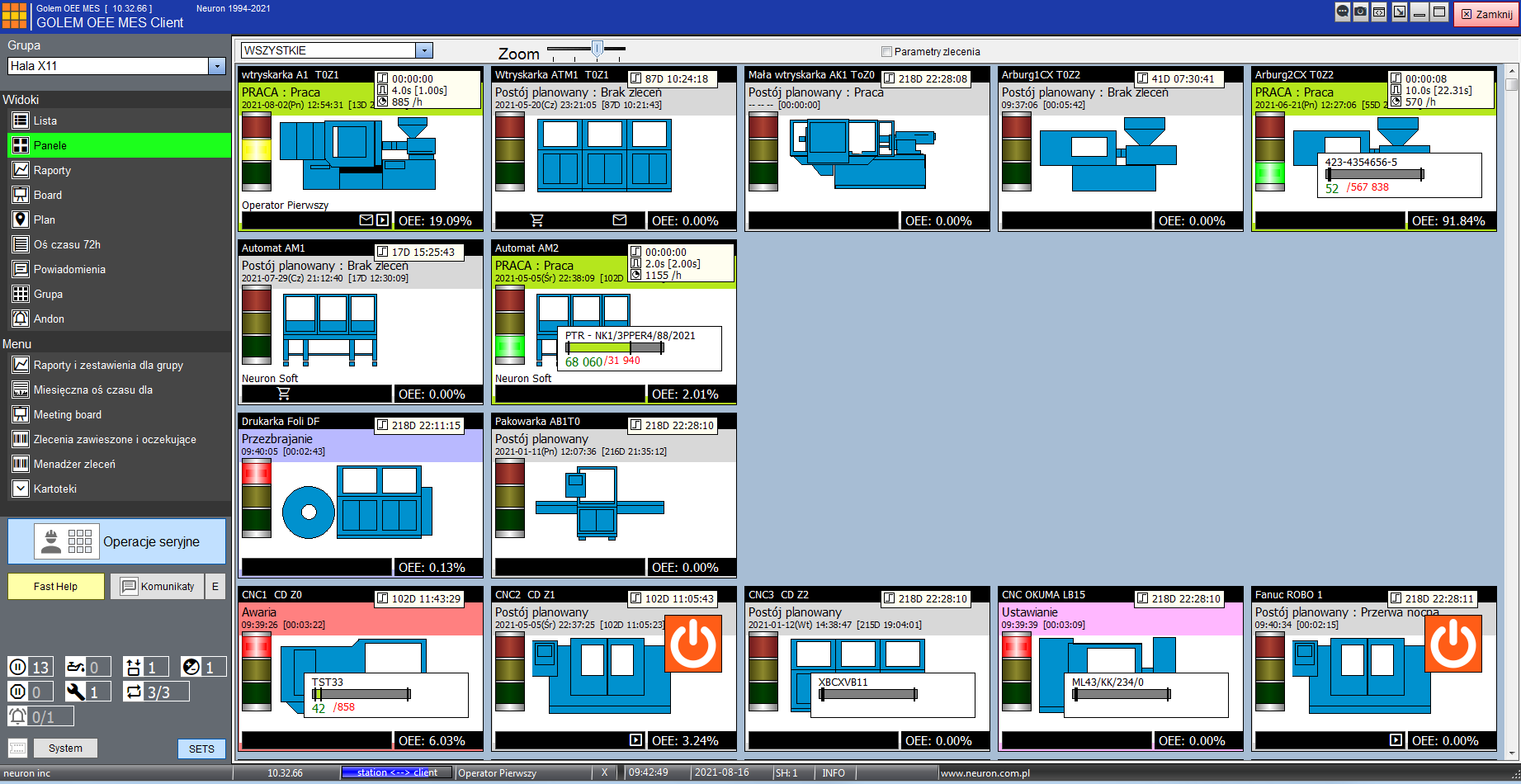
program kliencki systemu Golem OEE MES
Wynika to po części z pokrewieństwa z systemami SCADA, po części z faktu że wiele pierwotnie przypisanych takim systemom funkcji przejmują inne pakiety programów. Planowanie operacyjne przejmują systemy APS (Advanced Planning and Scheduling) współpracujące z systemami ERP/MRP w dziedzinie zabezpieczenia wszystkich zasobów a nie tylko czasu maszyny. Systemy WMS (Warehouse Management System) przejmują zadania związane ze śledzeniem przepływu materiałów, półproduktów i produkcji w toku a wspólnie z ERP/MRP rozliczają ten przepływ kosztowo.
Czy MES musi być zintegrowany z maszynami?
Oczywiście że nie. MES może się całkowicie opierać na interakcji z obsługą która za pomocą urządzeń mobilnych, czytników kodów itp. raportuje poszczególne etapy produkcji. Byle to nie było raportowanie hurtem wszystkiego raz na zmianę roboczą….Pamiętajmy jednak że największe straty powstają w wyniku kumulacji drobnych strat ciężkich do zauważenia a co dopiero do ręcznego zaraportowania.
Jedna minuta straty na godzinę dla maszyny w ruchu ciągłym to 744 minuty miesięcznie. Ponad 12 godzin, półtora zmiany roboczej. Jedna minuta.
Pomimo wysiłku obsługi zdeterminowanej aby je wyłapać i zarejestrować ( bo obsługa ma taką determinację, prawda ? ) najprawdopodobniej nic o tych 12 godzinach nie będziemy wiedzieli. A jeśli to 5 minut? Może nam zniknąć z pola widzenia 60 godzin.
Często systemy są hybrydą – dane pobierane są i z maszyn i z terminali operatorskich.
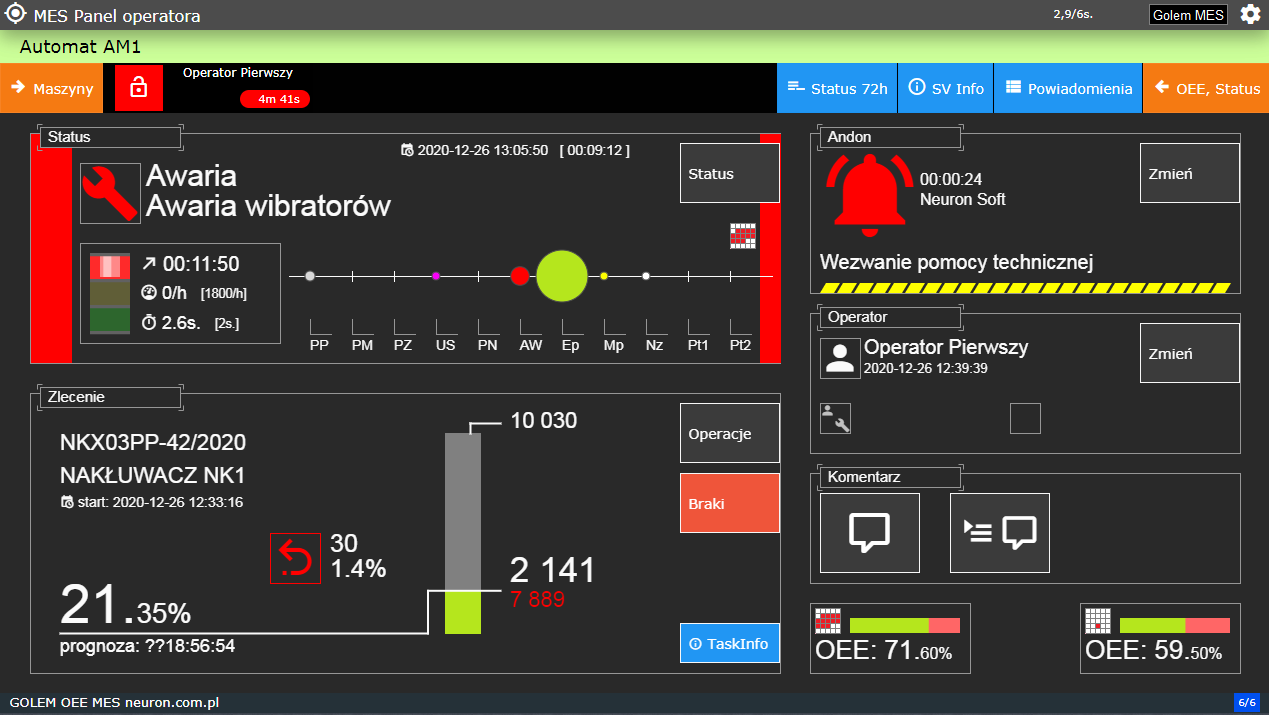
Golem OEE MES - panel dla operatora w wersji na tablet
W takim przypadku dużo danych wprowadzamy ręcznie ale są one skorelowane z pracą maszyny. Możemy zapytać operatora:
- dlaczego zaraportowałeś awarię o 12:43 skoro maszyna ostatni cykl zrobiła o 12:11 ?
Dane z maszyn
Przecież w maszynie jest "komputer" i ma gniazdo LAN więc o co chodzi ??No niestety tak pięknie to nie ma. Aby pozyskać dane takie jak my je chcemy widzieć musimy:
- Skomunikować się fizycznie ze sterownikiem PLC lub komputerem sterującym maszyny.
Często nie ma możliwości skorzystania z sieci LAN i trzeba skorzystać z tzw. sieci polowych (np. profibus) i stosownych konwerterów sprzętowych.
- Przetłumaczyć przesyłane dane stosując odpowiednie dla danego protokołu drivery / serwery OPC tak aby były dla nas czytelne. Często sieć LAN „transportuje” informacje w protokołach przemysłowych, np. EtherCAT.
- Wiedzieć jakie dane ( spod jakich adresów ) odczytać – bardzo rzadko są to dane przygotowane dla systemów MES. Najczęściej jedynie „podglądamy” zmienne których używają algorytmy sterujące maszyną.
- Przetworzyć dane. Widzimy licznik cykli. Ale nie wiemy kiedy był kasowany. A my chcemy znać licznik cykli od początku zmiany roboczej więc musimy „wyłapać” każdą jego zmianę i zwiększyć nasz licznik…
Problemy potęguje to że najczęściej mamy maszyny z różnych lat z różnymi systemami sterowania a wielu producentów żąda opłaty za dostęp do danych. A jak jeszcze nie żąda to będzie gdyż producenci odkryli nowe źródło dochodu….
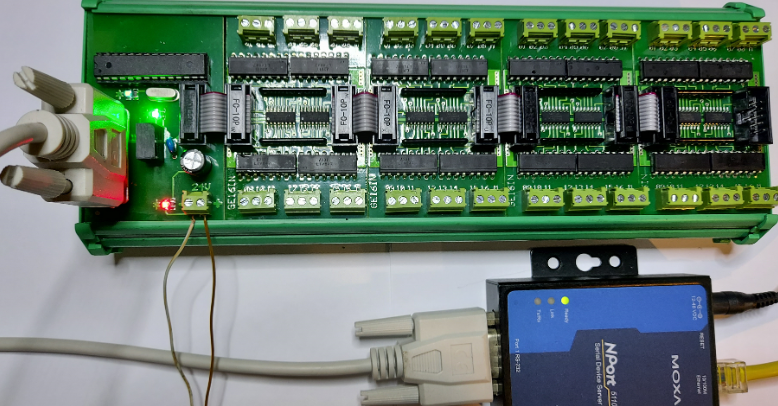
Golem - koncentrator GK64In i konwerter rs232/LAN - pozwala na podłączenie 64 sygnałów z wielu maszyn
Alternatywnym, często stosowanym rozwiązaniem, np. w naszym systemie Golem OEE MES jest
obserwowanie sygnałów dyskretnych, czy to zapożyczonych z maszyny czy zbieranych za pomocą dodatkowych czujników. Zresztą w wielu dużych aplikacjach w ten sposób podłączone są te maszyny z którymi nie udaje się skomunikować.
MES a IoT
Ponieważ pojawiają się głosy że niby nowoczesny system MUSI być oparty o IoT albo wręcz głosy że IoT jest alternatywą dla MES to wyjaśnijmy co to jest ten cały IoT …Za wikipedią: Internet rzeczy (ang. internet of things, IoT) – koncepcja, wedle której jednoznacznie identyfikowalne przedmioty mogą pośrednio albo bezpośrednio gromadzić, przetwarzać lub wymieniać dane za pośrednictwem sieci.
Czujnik wibracji z WiFi i adresem IP jest urządzeniem IoT. Czujnik wibracji z interfejsem Bluetooth LE który komunikuje się z masterem który ma WiFi tez jest urządzeniem IoT.
Maszyna CNC sterowana przez kontroler Sinumeric z doinstalowanym serwerem OPC UA też jest urządzeniem IoT. Cała maszyna jest urządzeniem a precyzyjniej węzłem IoT.
Możemy powiedzieć że IoT to sposób pozyskiwania danych dla systemów informatycznych który jest bliższy IT ( oparty na protokole TCP/IP i infrastrukturze sieciowej ) niż automatyce ( sieci polowe typu MODBUS, PROFIBUS, CAN ) a stwierdzenia że IoT jest lepsze od MES albo MES bez IoT jest przestarzały to objaw myślenia w kategoriach marketingu a nie techniki….
Maszyny z mikrosystemami MES
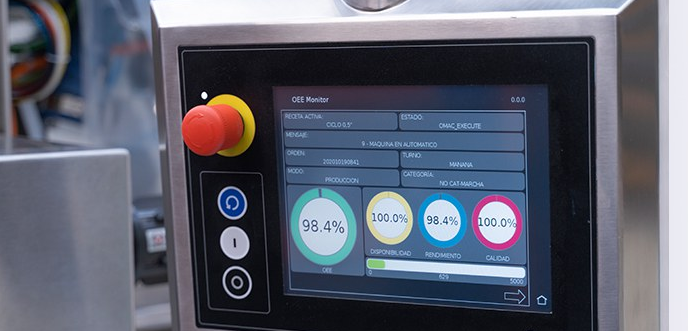
Systemy sterowania współczesnych maszyny mają coraz większą moc obliczeniową. Stało się więc możliwe wbudowanie do sterowania maszyny wielu funkcji charakterystycznych dla systemów MES. Logowanie pracy, wyliczanie OEE, liczenie na bieżąco wydajności i jej rejestracja.
Niektórzy nawet wieszczyli zmierzch systemów MES – przecież każda maszyna ma własny to po co globalny. Zapomnieli że szef produkcji nie ma czasu 8 razy dziennie obchodzić wszystkich maszyn. A nawet jeśli można to zrobić za pomocą aplikacji to kto by chciał mieć 20 różnych aplikacji…
Maszyny z takimi sterowaniami otwierają zupełnie nowe możliwości. Mogą one stanowić inteligentne węzły systemów produkcyjnych (IoT) do których można wysyłać zlecenia produkcyjne oraz można je prosić o informacje umieszczone w kontekście tych zleceń.
Monetyzacja czyli kup Pan dane
Jest wiele możliwości aby pobrać dane ze sterowników / komputerów maszyn. Jednak jak wspomniałem, producenci powoli zaczynają dostrzegać nowe źródło dochodów. Na razie głównie jednorazowych choć szybko to się może zmienić.W skrócie: chcesz czytać dane z maszyny to zapłać (płać) jej producentowi….
Jeśli maszyna ma sterownik z modułem sieciowym, np. serwerem OPC UA albo komputer CNC taki jak Sinumeric to producent maszyny nie musi robić nic. Wystarczy założyć hasło i je sprzedać.
Jeśli chce np. zastosować system subskrypcji albo podzielić dane na bezpłatne, np. dla robota IML i płatne dla systemu MES to musi się trochę napracować, ale da się.
Ponieważ firmy FAANG ( Facebook, Apple, Amazon, Netflix, Google ) nauczyły wszystkich że konfitury leżą w mikro płatnościach i odnawialnych subskrypcjach to wielu producentów maszyn pójdzie w tę stronę. Maszyny będą komunikowały się z ich chmurami, głównie na potrzeby tzw. predykcji a przy okazji staną się sklepami z danymi dla innych systemów.
Będą też oferować nie tylko surowe dane ale wszelkiego rodzaju analizy, aplikacje, pulpity etc. czyli opisane wyżej mikrosystemy MES, ale tylko dla swoich maszyn.
Oczywiście dane z naszych maszyn będą zanonimizowane i ich operator w żaden sposób nie będzie ich wykorzystywał tak jak firmy FAANG w żaden sposób nie wykorzystują informacji np. o lokalizacji telefonu względem lokalizacji reklamodawcy.
Swoją drogą ciekawie może być jak szef produkcji będzie chciał jakiś raport i dostanie komunikat: „subskrypcja dla obiektu 4567-4335-5456-6547 wygasła”
Ataki na systemy MES
Systemy MES narażone są na ataki. Ale nie mówimy tu o cyberatakach choć oczywiście w dobie rozwiązań chmurowych cyber bezpieczeństwo staje się podstawą. Im bardziej system jest rozproszony „w sieci” tym większe ryzyko że któryś z elementów stanie się obiektem ataku. Szczególnie ochrona krytycznej produkcji w niespokojnych czasach, ochrona przed wojskowymi botami może okazać się wyzwaniem.Systemy MES są jednymi z niewielu systemów narażonych na sabotaż. Wyrywanie kabli sieciowych, wyłączanie zasilania urządzeń, puszczanie maszyn „na sucho”, blokowanie czujników czy stwierdzenia w stylu: „ja wpisałem, pewnie nie było internetu” to takie mniej kreatywne zagrożenia działania pracowników którzy poczuli się systemem zagrożeni.
Bo choć, co ciekawe, w dłuższej perspektywie pracownicy zaczynają postrzegać korzyści z systemu ( często brali na siebie nie swoje winy ) to na początku zawsze uważają wdrożenie systemu jako zamach na swoją wolność.
MES a przemysł 4.0
Istota „Przemysłu 4.0” polega na stworzeniu inteligentnych łańcuchów wartości w oparciu o dynamiczne, samo organizujące się i optymalizujące się systemy socjotechniczne, określane mianem inteligentnych fabryk.
Tak kiedyś w swoim rządowym dokumencie napisali nasi zachodni sąsiedzi. Ale kto dziś o tym pamięta…W przyszłości MES będzie sterował przepływem informacji ale też przejmie proces decyzyjny. Dzisiaj dostarcza informacji dla menadżerów a ci w większym lub mniejszym stopniu, z większym lub mniejszym opóźnieniem przekładają tę wiedzę na optymalizację procesów.
Jutro system MES wspierany przez AI sam będzie podejmował decyzje w czasie rzeczywistym a menadżerowie będą jedynie określać warunki brzegowe.
MES będzie pobierał harmonogram z APS, przesyłał zadania do maszyn i systemów logistycznych, kontrolował ich wykonanie a w przypadku zakłóceń wewnętrznych lub zewnętrznych prosił APS o korekty które roześle do odpowiednich maszyn i zasobów.
Tak będzie jutro. No może pojutrze.
Dziś niestety koncepcja cyfryzacji przynosi czasami więcej szkody niż pożytku. Wiele firm zamiast skoncentrować się na „tu i teraz”, na wdrażaniu i optymalizowaniu znanych od lat narzędzi przyjęła pozycję wyczekującą na coś co będzie cool i super i jeszcze kasę na to dadzą….
Krótki przegląd funkcjonalności
W zasadzie większość produktów ma podobny zestaw funkcji choć ich implementacje potrafią się różnić diametralnie. Poniżej lista kilku z nich.Genealogia i identyfikacja produktu ( genealogy and traceability )
Genealogia to „badanie więzi rodzinnych jakie występują u ludzi na podstawie zachodzącego między nimi pokrewieństwa i powinowactwa”W przypadku produkcji mówimy o odwzorowaniu całego procesu w wyniku którego powstaje produkt. Może to być stosunkowo proste jeśli produkujemy plastikowe wiadra: tworzywo, barwnik, ustawiacz, forma, wtryskarka, operator, paleta z produktem. No jeszcze uchwyty i jakieś nalepki. Albo nadruk na tamponiarce, więc paleta nim trafi na magazyn wyrobów gotowych musi odwiedzić dział nadruków.
Gorzej jak produkujemy skomplikowany produkt który składa się z wielu skomplikowanych półproduktów których część kupujemy a część sami produkujemy.
Z kolei identyfikacja ( traceability ) pozwala nam na analizę każdego z węzłów zdefiniowanych w genealogii dla konkretnego produktu lub partii produktu.
Powiedzmy że w partii produkowanych szaf odpadają drzwi. Możemy sprawdzić kto, kiedy na jakich frezarkach obrabiał drzwi i boki szaf z wadliwej partii oraz z jakiej partii płyt MDF i na jakich piłach formatowych je pocięto.
Harmonogramowanie produkcji
Wróćmy do naszych wiader. Harmonogram produkcji pozwala nam na zaplanowanie kiedy i na jakiej maszynie będziemy je robić, zagwarantować dostępność ustawiacza do zmiany formy, sprawdzić dostępność materiału a jeśli na wiadrach będą nadruki to powiązać zadanie produkcyjne dla wtryskarki z zadaniem produkcyjnym dla tamponiarki.Harmonogram produkcji dostarcza też „punktów odniesienia” które pozwalają systemom MES odnieść się do nich w swoich pomiarach.
Najbardziej zaawansowane systemy mogą posiadać sprzężenie zwrotne, np. korygować harmonogramy po wystąpieniu zakłóceń produkcji takich jak awarie.
Genealogia, identyfikacja i harmonogramowanie to trzy najbardziej złożone funkcje które często są delegowane do innych systemów a MES jedynie z nimi współpracuje.
To funkcje które albo nie są implementowane albo są implementowane z różnymi ograniczeniami. Tym bardziej że implementować muszą one skrajnie inne potrzeby i czym innym będą w przetwórstwie tworzyw a czym innym w przemyśle maszynowym.
Monitorowanie postojów maszyn

widok zmienności stanu maszyny z ostatnich 72 godzin z krokiem 4 minut
Każda maszyna ma okresy w których nie pracuje, nie produkuje, ma przestój. Czasami jest to przestój planowany, nie pracuje bo nie ma dla niej zadań a czasami jest to dłuższe zakłócenie w pracy, np. awaria. Dlatego wręcz elementarną funkcją jest rejestracja każdego postoju z czasem, udziałem procentowym i w miarę możliwości komentarzem obsługi. No i ich analiza, określenie które z nich są stratami a które nie. Które są nieuniknione, które incydentalne a które wymagają udoskonalenia procesu.
Pamiętać też należy że wskaźnik OEE nie bierze się z powietrza. Jakość rejestracji przestojów decyduje o jakości takich składników jak czas zamówiony, czas operacyjny i dostępność.
Monitorowanie wydajności i produktywności maszyn
Źródłem najtrudniejszych do zbadania strat są spadki wydajności i mikropostoje. Tu kilka minut, tam kilka, tam tempo spadło o kilka procent na kilkadziesiąt minut. Straty tak małe że w pojedynkę ujdą uwadze najlepszemu obserwatorowi.
aktualny czas cyklu oraz czasy cyklu i wydajności dla różnych stanów maszyny w ramach np. zlecenia
Dlatego kluczowym jest pomiar czasu cyklu i wydajności umieszczonej w odpowiednim kontekście. Można pracować z dużą wydajnością i częstymi problemami. Można też pracować bardziej produktywnie optymalizując tempo pracy tak aby ograniczyć występowanie problemów.
Weryfikacja realizacji zadań/zleceń produkcyjnych
Jakość planowania czy harmonogramowania produkcji zależy od wielu czynników. Jednym z nich jest znajomość zdolności produkcyjnych parku maszynowego oraz świadomość możliwych zakłóceń które powodują że dwa identyczne zlecenia realizowane są w różnym czasie.Jeśli mamy dwie podobne maszyny ale o różnym stopniu zużycia przekładającego się na awaryjność czy szerzej spadek dostępności to nie możemy stosować dla nich takich samych kryteriów podczas planowania.
Poza stanem technicznym na czas realizacji zleceń produkcyjnych, szczególnie na różnice w czasie wykonania identycznych zleceń z identycznymi wolumenami ma np. wyszkolenie obsługi, logistyka, skomplikowana lub trudna technologia.
Dlatego tak ważna jest możliwość śledzenia, rejestrowania i analizy rzeczywistej realizacji zadań/zleceń.
Zarządzanie jakością
Kontrola jakości i analiza przyczyn powstawania wadliwych wyrobów to jedna z podstawowych funkcji każdego systemu produkcyjnego. System MES może zbierać informacje o ilości braków i ich rodzaju ( np. z systemów wizyjnych ) przyporządkowując do produktów, zleceń, maszyn, stanowisk czy operatorów.System może też zbierać dane dla statystycznej kontroli procesu ( SPC ) albo wręcz taki system implementować.
Wskaźniki KPI
Najważniejszym KPI w przemyśle jest wskaźnik OEE. System powinien wyliczać wskaźnik w czasie rzeczywistym, np. dla aktualnej zmiany czy aktualnego zlecenia oraz dla dowolnych danych historycznych, szczególnie dla dowolnego zlecenia produkcyjnego.OEE jest o tyle ważny że stanowi on swego rodzaju skompresowany obraz rzeczywistości. Jeśli niepokoi nas jego spadek to możemy się „cofnąć” aby przeanalizować dane z których się on wywodzi. Codzienna analiza danych źródłowych przy obecnej ich ilości jest coraz trudniejsza i musimy wiedzieć kiedy jest ona uzasadniona.
Innymi wskaźnikami są np. TEEP pomocny w planowaniu czy wskaźniki MTTR MTBF dla utrzymania ruchu.
Zobacz Wskaźnik OEE
Wizualizacja pracy i monitowanie o problemach (Andon)
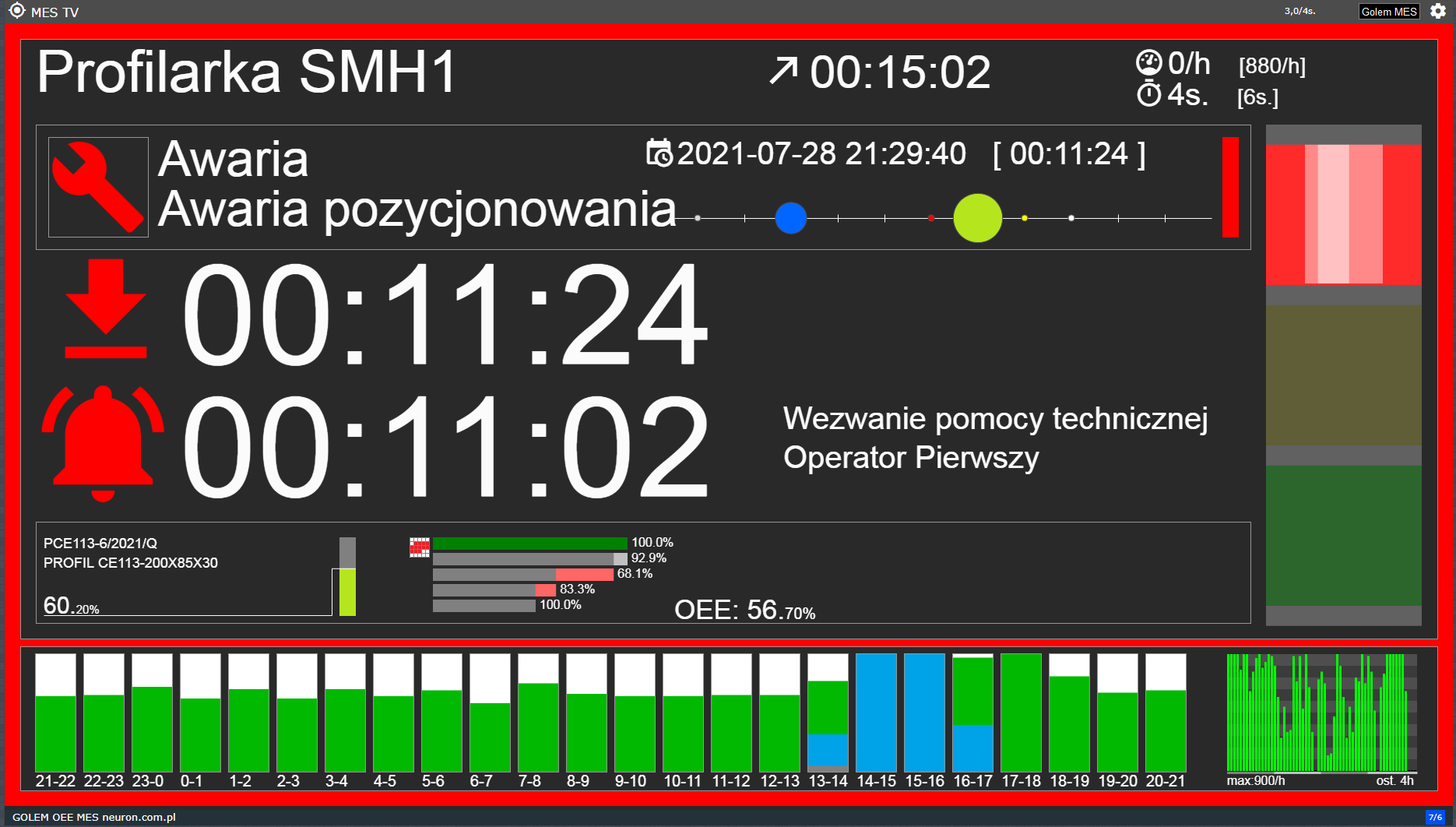
Wizualizacja awarii i wezwania andon na duzym monitorze.
Jedną z wartości dodanych jest możliwość zobaczenia w dowolnym momencie z dowolnego miejsca
jaki jest stan maszyn. Ich status, postęp realizowanego zlecenia, aktywność. To taka cyfrowa wersja Gemba Walking – „Idź i zobacz” choć nigdzie nie trzeba chodzić. Z kolei Andon to z japońskiego „widoczny znak”. To podsystem za pomocą którego pracownik powiadamia wszystkich zainteresowanych o zaistniałych problemach. Można go traktować jako system przywołania pomocy ale głównie chodzi o to aby żaden problem nie pozostał niezauważony.
Prezentacja na osi czasu
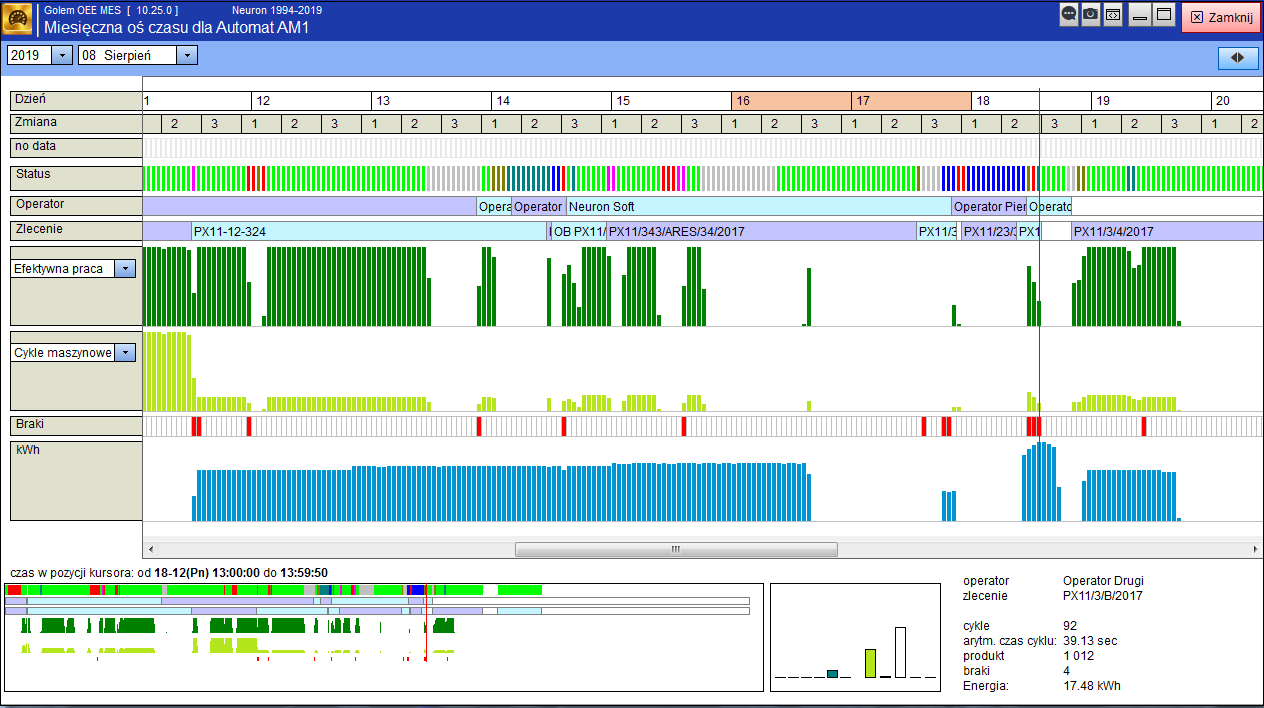
Praca maszyny ( praca, postoje, wydajność, braki, pobrana energia, zlecenia produkcjne) rozpisana na poszczególne godziny w miesiącu
Mówi się że jeden obraz jest wart więcej niż 1000 słów. Zasadę tę doskonale implementują wszelkie wykresy pracy rzutowane na oś czasu. Jeden rzut oka pozwala stwierdzić że maszyna w nocy nie pracowała przez 2 godziny i trzeba wejść w szczegóły aby dojść dlaczego.
Wsparcie dla utrzymania ruchu
UR dysponuje własną klasą oprogramowania, oprogramowaniem CMMS. Jednak coraz częściej systemy MES i CMMS współpracują ze sobą.System MES dostarcza informacje które mogą wspomóc prewencję – analiza postojów, spadków wydajności, zwiększonej ilości wad pozwala na optymalizację planów przeglądów okresowych i ich synchronizację z planami produkcyjnymi.
Zużycie mediów
Ważną funkcją jest monitorowanie zużycia mediów: powietrza, pary, gazów, wody a nader wszystko energii elektrycznej. I nie mówimy tu tylko o informacji o tym ile danego czynnika zużyto np. w formie miesięcznego wykresu. Mówimy o analizie zużycia danego medium w funkcji zlecenia, produktu, stanu maszyny.Wiele maszyn zużywa energię elektryczną nie tylko wtedy gdy wykonują konkretną pracę ale też w trakcie przezbrajania, ustawiania, zatrzymania a nawet postoju. Po skończonej partii produktu nie opłaca nam się wyłączyć maszynę bo zaraz będziemy musieli ją znowu rozgrzać. Jednak to „zaraz” to może być za wiele godzin wiec wiedza ile prądu zużyto podczas pracy, ile podczas postoju planowanego a ile podczas ustawiania czy wręcz awarii jest bezcenna.
Przepływ i zużycie materiału
System MES, szczególnie w kolaboracji z systemem WMS może nas wspomóc w określeniu zużycia surowców i komponentów oraz w zarządzaniu „magazynami” przy maszynach. Często jest tak że niektóre komponenty są dostarczane partiami i system powinien nam wyeliminować konieczność oczekiwania na ich uzupełnienie.Przepływ ( zużycie w funkcji czasu ) materiału przez konkretną maszynę może nieść też szereg informacji istotnych z punktu widzenia zachowania reżimów technologicznych i jakości.
Kompletny system produkcyjny powinien nie dopuścić do rozpoczęcia zleceń produkcyjnych jeśli nie ma odpowiedniej ilości wszystkich surowców i materiałów, oraz alarmować o ich zbliżającym się wyczerpaniu.
Udostępnianie dokumentacji
Głównym zadaniem jest nie tyle zarządzanie dokumentacją produkcyjną co jej udostępnianiem w odpowiednim czasie odpowiednim osobom. Tak aby operator nie musiał się zastanawiać czy załadował właściwe etykiety, jak pakować produkt na paletach czy jak ustawić maszynę dla danego zlecenia.Kilka innych funkcji
- Zarządzanie narzędziami produkcyjnymi typu formy, wykrojniki etc
- Monitorowanie zużycia mediów w kontekście realizacji produkcji
- Monitorowanie zużycia surowców i materiałów
- Zarządzanie podręcznymi magazynami ( marketami ) przy maszynach
- Zarzadzanie programami maszyn, np. CNC
No dobrze, ile to kosztuje
Dobry spec od marketingu odpowiedziałby: A ile kosztuje brak systemu MES ?no coś w tym jest ….
Musimy rozgraniczyć pomiędzy małymi, czy może bardziej precyzyjnie samodzielnymi systemami a tymi które stanowią integralną część kompletnego systemu produkcyjnego.
Te pierwsze można wdrożyć w ramach pojedynczego, spójnego projektu. Mogą być całkowicie niezależne od innych systemów albo współpracować z systemami ERP w sposób ograniczony, np. do importu listy zleceń.
W ich przypadku można dość precyzyjnie określić koszty na wczesnym etapie. Np. podłączenie maszyny do systemu Evocon to 490euro za czujniki plus 190euro miesięcznie za maszynę.
W przypadku naszego Golema dostępny jest oficjalny cennik licencji i sprzętu i można oszacować że system dla 30 maszyn to jednorazowy wydatek od 8 tyś PLN (licencje, koncentratory, przekaźniki, okablowanie). Plus koszt integracji którą klient może wykonać samodzielnie lub zapłacić integratorom.
W przypadku dużych systemów sprawa nie jest ani prosta ani oczywista a każda wycena obarczona jest sporym ryzykiem. Liczne licencje, dużo roboczogodzin często wymagających fizycznej obecności. Koszty pozyskania informacji z maszyn. Koszty szkolenia, stworzenia dokumentacji, kastomizacji, indywidualnych rozwiązań.
A nader wszystko koszty integracji z systemami, np. ERP.
Do tego nigdy nie da się określić wszystkich potrzeb. Zamawiający nie do końca wie czego chce a wykonawca nie do końca wie co „zastanie” a obie strony często zbyt dosłownie traktują marketingowe zapewnienie „dopasowujemy się do potrzeb klienta”.
Zresztą często w takich projektach jest więcej niż jeden dostawca a więc prędzej czy później pojawią się spory kompetencyjne.
No i czas. Czas też jest kosztem a im większy system MES tym więcej czasu będzie trwało jego wdrożenie. Kiedyś w jednej firmie uruchomiono naszego Golema w mniej niż miesiąc. Potem „centrala” nakazała zmianę systemu. Trwało to cztery lata. Nie, nie po czterech latach zmieniono system. Cztery lata minęły od decyzji do jego pełnego wdrożenia. I nie jest to wcale jakiś skrajny przykład – czasami przygotowanie oferty trwa wiele miesięcy.
Jak wdrożyć system
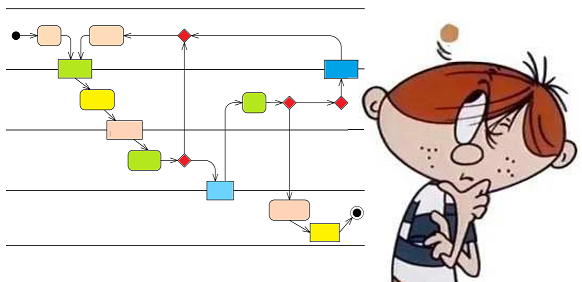
Najpierw trzeba odpowiedzieć na podstawowe pytanie: jakie są nasze doświadczenia. Nie tyle wymagania co właśnie doświadczenia. Powyższy tekst powstał nie dla uciechy autora ale dla tego że każdy zapytany „co to jest MES” odpowie cos innego.
A kto wie co to jest WMS ? Ręka do góry. Kto wie co się dzieje a co się dziać powinno jak operator kończy zlecenie i trzeba zwrócić na magazyn niewykorzystane etykiety? No właśnie …
Sprawa jest prosta jeśli nie mamy nic i chcemy zacząć od prostego monitoringu pracy maszyn i realizacji zleceń. Nawet jeśli wdrożone rozwiązanie nie spełni wszystkich naszych oczekiwań to będziemy wiedzieć których i dla czego a to wiedza bezcenna gdy zdecydujemy się na „kolejny krok”.
Najbardziej ryzykowne podejście: nie mamy nic ale chcemy aby ktoś zrobił nam duży w pełni funkcjonalny system. Taki który będzie integrował w sobie dane z wielu systemów, który zaimplementuje harmonogramowanie i traceability i inne cuda. Najlepiej na bazie już istniejących systemów no bo przecież system ERP służy nam już 15 lat i nie będziemy go zmieniać.
Pamiętajmy też że dostawcy rozwiązań mają dużą wiedzę w swoich dziedzinach i niemałą w dziedzinach pokrewnych. Jednak to klient musi wiedzieć czy, jak i w jakim obszarze poszczególne systemy mają współpracować ze sobą. Musimy wiec potrafić uzgodnić wymagania pomiędzy nimi, często nie mając ku temu kompetencji.
Dlatego warto rozważyć wesparcie niezależnych konsultantów takich jak firma ABIT którzy potrafią widzieć całość procesów.