EAM
Zaczniemy od wyjaśnienia czym jest EAM który często wymieniany jest razem lub zamiennie z CMMS. EAM - Enterprise Asset Management - zarządzanie majątkiem firmy.CMMS i utrzymanie ruchu kojarzone jest najczęściej z maszynami. Współcześnie jednak coraz częściej zadania i systemów informatycznych i pracowników UR rozciągają się na całość majątku - budynki, pojazdy, infrastruktura energetyczna.
EAN to też synonim ogólnej strategii kompleksowego zarządzania majątkiem od planów zakupowych, przez eksploatację aż po utylizację. Możemy powiedzieć że CMMS jest ( może być ) podsystemem systemu EAM
Dyrektywa maszynowa
Dyrektywa maszynowa to zbiór wymagań zasadniczych stawianych producentom i użytkownikom maszyn w zakresie ich konstrukcji i bezpieczeństwa.Czy dyrektywa mówi coś na temat oprogramowania CMMS? Nie. Dlaczego wiec ją przywołujemy? Bo to jej pojawienie się w roku 2006 spowodowało że jakieś tam CMMS’y przestano postrzegać jako zbędną „fanaberię” a jako narzędzie wspomagające realizację wymagań dyrektywy.
Mniej więcej w tym samym czasie zaczęły się popularyzować wskaźniki KPI takie jak OEE które pokazały menadżerom że jest takie coś jak dostępność i że cos jednak od tych gości z kluczami i miernikami jednak zależy i być może jakeś wsparcie dla nich ma sens.
Niby takie same a takie różne
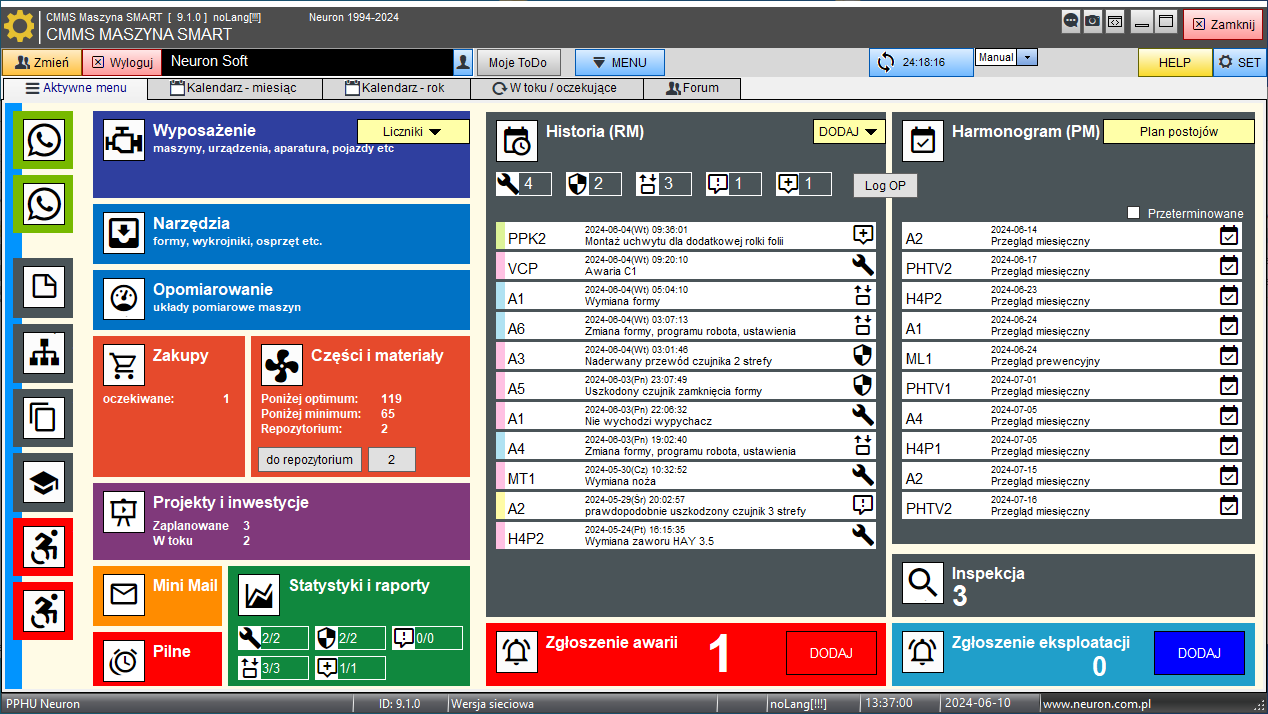
program cmms maszyna smart - aktywne menu
Oprogramowanie CMMS jest o tyle ciekawe że każda z implementacji ma bardzo podobny zestaw modułów/funkcjonalności. Czy CMMS Maszyna SMART , Agility, SAP PM czy IBM Maximo, każdy z nich ma podstawowe moduły takie jak zarządzanie wyposażeniem, historia zdarzeń, planowanie PM, wizualizacje, zarządzanie bezpieczeństwem, zapasami i zakupami itd. Jak to mówią: diabeł tkwi w szczegółach”…
Różne implementacje, różne technologie, różny poziom komplikacji, różne pojmowanie i zrozumienie celów no i różne koszty. Różne są też zależności pomiędzy modułami czy możliwości współpracy w ramach spójnych systemów produkcyjnych.
Ponadto duże systemy należy traktować jako platformy które przez wdrożeniowców zostaną tak ukształtowane i skonfigurowane jak sobie tego życzy klient. Tyle że klient nie zawsze wie czego sobie życzyć, prace liczone mogą być w setkach godzin a jedna godzina może kosztować tyle co pół kosztu licencji naszego CMMS’a
Korzyści
Każdy materiał promocyjny akcentuje korzyści z wdrożenia systemu. Wiele z nich to poważne koszty więc klient, szczególnie ten który płaci musi mieć przeświadczenie że inwestycja się zwróci.Czy samo oprogramowanie CMMS spowoduje redukcję ilości i kosztów awarii, że harmonogramy nie dość że się będą same tworzyć to jeszcze będą się „spinać”? Spowoduje że zapasy będą optymalne i nikt nigdy nie będzie szukał deklaracji CE i DTR’ki gdy przyjdzie PiP? No nie.
Tego mogą dokonać ludzie odpowiedzialni za szeroko rozumiane utrzymanie ruchu.
Oprogramowanie ma im w tym pomóc. Uprościć pracę, wspomóc komunikację, odrobinę zdyscyplinować. Pomóc w lokalizowaniu problemów czy optymalizacji kosztów dzięki analizie zebranych informacji.
Kto jest użytkownikiem systemu CMMS ?
Pierwszą grupą są mechanicy, elektrycy, automatycy, mechatronicy. Wszyscy ci od których codziennej pracy, wiedzy, doświadczenia, intuicji i zaangażowania zależy wszystko, choć stare przysłowie mówi „że zależy od nich wszystko a na nic nie mają na nic wpływu”CMMS powinien wspierać i w miarę możliwości organizować ich pracę, dostarczać wiedzę, wgląd w historię, wspierać komunikację.
Druga grupa to pracownicy produkcyjni. Ich rola najczęściej ogranicza się do dostarczania informacji o awariach, ale zgodnie z duchem systemu TPM mogą np. dokonać wstępnej diagnozy oszczędzając czas osób z pierwszej grupy.
Trzecia grupa to osoby zarządzające UR. Ich rola jest szeroka, od dbania o wszystkie aspekty prawne, planowanie pracy, zagwarantowanie zasobów takich jak części, materiały, wykwalifikowany personel, gaszenie konfliktów produkcja – UR ( a najlepiej wdrożenie filozofii TPM aby nie było podstaw do konfliktów ) no i przekonywanie decydentów że to wszystko jest ważne i warto w to inwestować.
Czwartą grupę osobiście nazywam „zarządzającymi z oddali”. Koordynatorzy, audytorzy, ludzie którzy z racji swoich szerokich obowiązków nie mają czasu pochylać się nad szczegółami ale chcą wiedzieć aby wspierać ale też oceniać.
Często domagają się prostych odpowiedzi na skomplikowane pytania. Chcą, wróć, nie chcą, żądają jednego kompletu wskaźników KPI dla WSZYTSKICH maszyn i urządzeń. A co gorsza, czasami dla wszystkich pracowników.
Zarządzanie majątkiem - najpierw trzeba wszystko spisać
Podstawowymi modułem jest rejestr wyposażenia w którym spisujemy cały nasz majątek techniczny. Wyposażeniem może być maszyna, urządzenie, narzędzie, pojazd czy cały budynek. To wokół tego wyposażenia wszystko się "kręci".Każda firma ma gdzieś spis całego majątku, głównie na potrzeby księgowe ale dopiero jak zaczniemy wszystko wprowadzać do systemu zaczynamy pojmować jak rozległy to majątek.
Gdy zaczynamy dzielić wyposażenie wg przeznaczenia, miejsca, wartości czy ważności zaczynamy sobie uświadamiać że w firmie mamy 37 klimatyzatorów, a właściwie to 37 „końcówek” wchodzących w skład 3 niezależnych systemów klimatyzacji nie licząc rozległego systemu chłodzenia wody technologicznej.
Ważna jest jednoznaczna identyfikacja wyposażenia. Każdy obiekt ma wiele identyfikatorów takich jak symbol, numer seryjny, inwentarzowy, udt. Ważne jest jednak aby każdemu obiektowi a w szczególności każdej maszynie nadać jednoznaczne, krótki i proste oznaczenie które przyswoją sobie wszyscy pracownicy. Tak aby nikt w firmie słysząc o prasie PH3 nie miał wątpliwości o jakiej maszynie mowa.
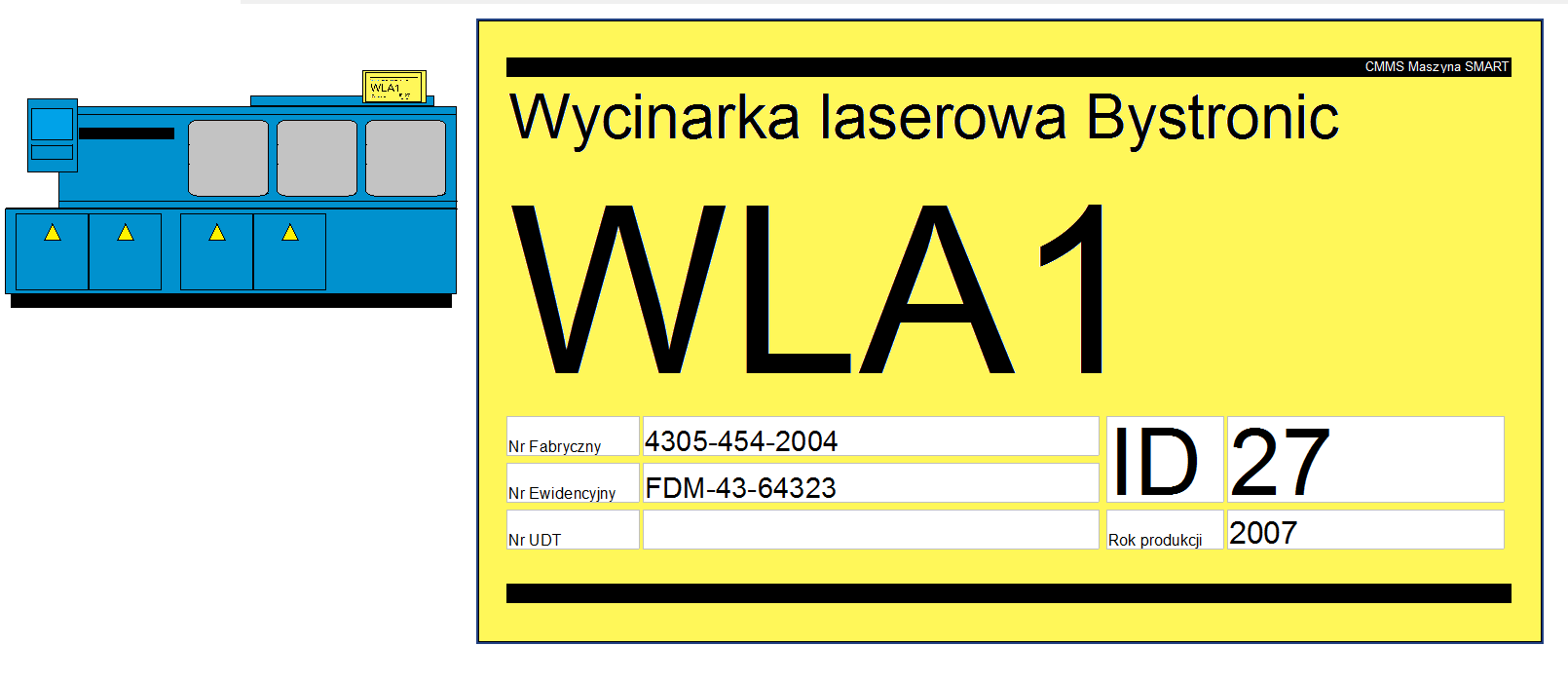
Podziały, grupy, klasyfikacja ABC
Jako że wyposażenia może być bardzo dużo to pamiętać trzeba o jego właściwym pogrupowaniu pożytecznym przy szukaniu i filtrowaniu. Przypisaniu do wydziałów, pogrupowaniu według rodzaju, przeznaczenia, lokalizacji. Wiele programów CMMS stosuje hierarchie wyposażenia opartą o drzewa:zakład >> wydział >> linia produkcyjna >> profilarka PR4
choć z drzewami jest jednak taki problem że zawsze mamy „coś” co pasuje nam do wielu gałęzi.
Popularna jest też klasyfikacja ABC określająca „ważność” maszyny która może decydować o kolejności obsługi gdy przydarzą się problemy w tym samym czasie i musimy zdecydować gdzie rzucić ograniczone zasoby.
Dokumenty i zasoby
Nieodzownym elementem spisu wyposażenia jest spis przypisanych dokumentów. I tych które posiadamy i tych których nie mamy choć powinniśmy mieć.Każda maszyna musi posiadać ( zgodnie z dyrektywą maszynową ) deklaracja zgodności CE, instrukcję BHP oraz dokumentację techniczno-ruchowa. Dokumenty te są szczególnie ważne że gdy nawiedzi nas kontrola PiP bo ich brak może mieć niemiłe konsekwencje. Brak albo fakt że nie możemy ich znaleźć.
Dysponujemy też dużą ilością innych dokumentów, dokumentacji, pakietów z programami etc. które również wymagają zaewidencjonowania i powiazania z naszym wyposażeniem.
Strategia utrzymania ruchu
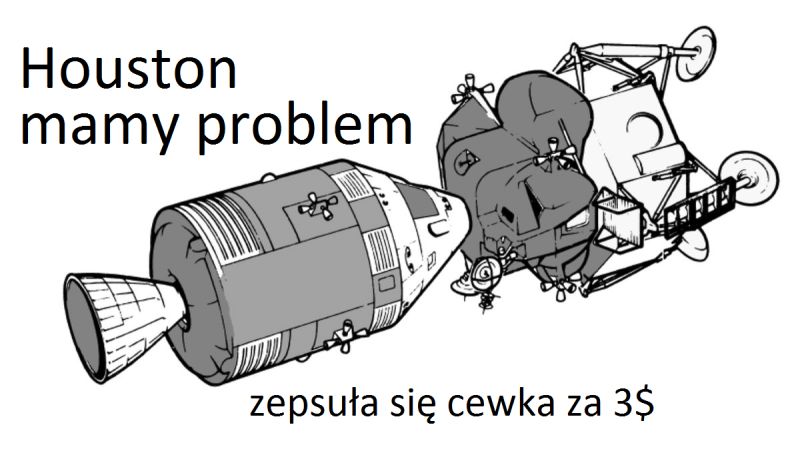
RM - Strategia reaktywna ( Reactive Maintenance )
Strategia polegająca na reagowanie na występujące zdarzenia. Naprawiamy maszyny gdy się zepsują.Strategia odsądzana od czci i wiary, z taką domniemaną narracją że wy tutaj towarzysze nic nie robicie tylko czekacie na awarię a przecież w firmach zarządzanych zgodnie z linią partii awarie nie występują, wystarczy wprowadzić inne, te lepsze strategie …
Dlatego musimy rozgraniczyć pomiędzy reakcją na awarię których nigdy w pełni nie unikniemy, pomiędzy brakiem prewencji co się dziś rzadko zdarza i pomiędzy celową strategią zwaną „run to failure”.
Ta ostatnia jest w wielu przypadkach najlepszym wyjściem bo nie będziemy robić comiesięcznych przeglądów żarówek bo to bez sensu. Lepiej mieć ich zapas i odpowiednią drabinę.
PM – Strategia prewencyjna ( Preventive Maintenance )
Strategia oparta na planowanych, często powtarzalnych czynnościach technicznych mających na celu utrzymanie i odbudowę sprawności technicznej urządzeń.Strategia PM od wielu lat jest standardem i nie trzeba do niej w dzisiejszych czasach nikogo przekonywać. Gorzej jest z ich skutecznością i celowością bo planowanie i realizacja przeglądów technicznych to ciężka praca.
PdM – Strategia predykcyjna ( Predictive Maintenance )
Predykcja to nic innego jak przewidywanie przyszłości na podstawie doświadczeń wspartych obserwacjami i pomiarami. Predykcja nie jest strategią zastępującą w jakikolwiek sposób inne strategie, jest ich uzupełnieniem.Predykcją jest nie tylko stosowanie nowoczesnych technologii ale też zwykła, codzienna, inżynierska praca polegająca na analizie historii i stanu aktualnego co przełożyć się powinno na bardziej elastyczne planowanie.
Dlaczego nie lubimy awarii
No wiadomo, straty, koszty, dezorganizacja pracy. Ale dlaczego my, architekci systemów CMMS, specjaliści od LEAN i zarządzania, szkoleniowcy, zarządzający „z oddali”, dlaczego my tak nie lubimy awarii?Bo nam psują nasze misterne plany. Miało być tak pięknie, pracownicy mieli zrobić to i to, miało im to zająć tyle a tyle czasu, mieliśmy to ładnie podsumować i ocenić. A tu błysk za lasem, wszystkie maszyny się zatrzymały, 12 nie można załączyć i wszystkie dzisiejsze plany popłynęły ……..
Niestety bez względu na przyjęte strategie i włożony wysiłek awarie zawsze będą nam komplikowały życie dlatego zawsze musimy być gotowi na coś na co przygotować się nie sposób.
Zlecenie pracy
Tu musimy sobie wyjaśnić pewne pojęcia które często są albo niedoprecyzowane albo źle interpretowane. Ogólnie pracę UR możemy podzielić na:- Prace prewencyjne zaplanowane na „kiedyś”, o tym niżej będzie cały rozdział
- Prace interwencyjne ( reaktywne ) czyli wszelkie usterki, awarie, drobne modyfikacje
- Prace eksploatacyjne – nie mieszczą się one w konwencji UR ale pracownicy UR je wykonują, np. zmiana wyposażenia maszyny przy zmianie produkcji zwane potocznie przezbrojeniem maszyny
- Prace inwestycyjne, np. zbudowanie jakiegoś urządzenia „we własnym zakresie”
Dla czynności planowanych takich jak przeglądy PM wystawiamy zlecenia co jest naturalne i pożądane. Gorzej z pracami reaktywnymi. Jedne systemy je tylko rejestrują, inne wystawiają zlecenia na wykonanie takich prac a jeszcze inne rejestrują ale nazywają rejestrację zleceniami pracy.
Rozliczenie czasu pracy
Optymiści wyposażyli systemy CMMS w zlecenia pracy bieżącej pozwalające na planowanie obsługi awarii. Pękł kolektor, leje się woda ale STOP. Najpierw zlecenie. A w sumie to 3 zlecenia bo przecież lecimy tam w trójkę. Ewentualnie dopuszcza się wystawienie zleceń post factum.Ale po co zlecenia pracy? Czy nie wystarczy zarejestrowanie awarii czy podobnych zdarzeń losowych? Nie jeśli zależy nam na rozliczaniu czasu pracy pracowników.
Panuje przeświadczenia że obsługa awarii to prosty proces: cos się zepsuło, ktoś poszedł, naprawił i wrócił. Tak czasami bywa ale często rzeczywistość jest bardziej skomplikowana.
Piątek, godzina 12:05 uszkodziła się przekładnia. Mechanik M1 demontuje napęd i na warsztacie ją wymienia. Przez 2 godziny bo kończy pracę. Pomaga mu elektryk E1 który musi odłączyć silnik co mu zajmuje 20 minut.
W poniedziałek o 6:15 mechanik M2 kończy pracę swojego kolegi co też zajmuje mu 2 godziny. Pomaga mu elektryk E2 przez 30 minut. Jedna prosta awaria zaangażowała 4 osoby w różnym czasie i wymiarze czasu.
Jedna awaria a my musimy wystawić cztery zlecenia dla czterech osób i precyzyjnie opisać ich pracę.
Dzięki temu będziemy wiedzieli ile w danym miesiącu pracował M1 a ile M2, a nawet sprawdzimy który z nich, M1 czy M2 szybciej naprawia maszyny.
Czy to się może udać? Z pewnością, ale wymaga to żelaznej konsekwencji lub zatrudnienia dodatkowej osoby, dyspozytora który będzie kierował pracą kolegów i wystawiał im zlecenia. Inaczej okaże się że w tym samym ośmiogodzinnym okresie mechanik M1 pracował 6 godzin a mechanik M2 11 godzin….
Najczęstszą przyczyną fiaska wdrożeń systemów CMMS jest „księgowe” podejście do pracy i kosztów przy jednoczesnych próbach chodzenia na skróty w opisywaniu rzeczywistości.
O jak skomplikowanych procesach mówimy przeczytasz w naszym artykule: Ile czasu trwa naprawa maszyny
Można inaczej
W naszym programie CMMS Maszyna SMART zaimplementowaliśmy odmienną filozofię. Do każdego zdarzenia, każdej pracy przypisana jest jedna osoba odpowiedzialna.Uważamy że zarządzający UR powinni oceniać pracę swoich ludzi przez pryzmat ich indywidualnych umiejętności i towarzyszących ich pracy okoliczności a nie na podstawie suchych liczb.
To że mechanik M1 pracuje średnio dwa razy dłużej nad jedną awarią czy przeglądem niż mechanik M2 nie musi wcale oznaczać że jest mniej kompetentny czy bardziej leniwy. Wręcz przeciwnie, może oznaczać że jego umiejętności predysponują go do najbardziej skomplikowanych a więc pracochłonnych prac.
Historia zdarzeń
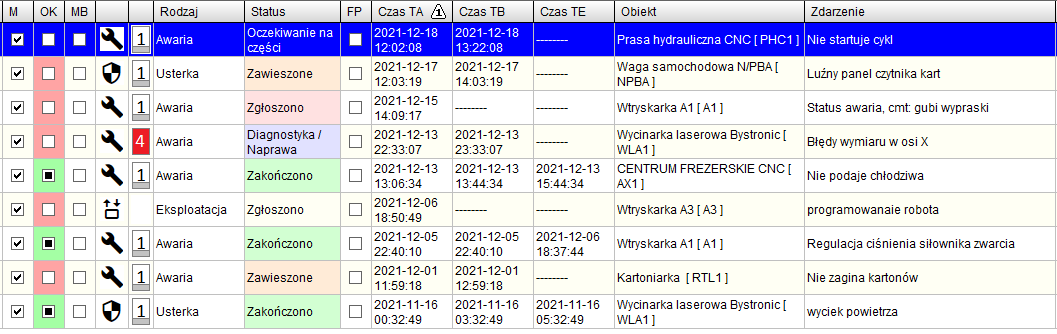
Każda awaria, usterka, każda drobna praca powinna być szczegółowo opisana. Każda przypisana do konkretnego obiektu oraz oznaczona szeregiem parametrów określających rodzaj, czas, wagę. Pamiętajmy że taka baza może mieć wiele tysięcy rekordów dlatego istotna jest możliwość filtrowania po czasie, po obiekcie ( grupie obiektów ) po rodzaju i wadze zadań, po ich statusie
Po co nam historia ?
- Aby mieć wgląd w sprawy bieżące, np. awarie w toku, awarie z ostatnich dni
- Aby mieć świadomość skali problemów
- Aby mieć materiał do analiz stanu technicznego maszyn bez którego ciężko planować sensowne prace okresowe
- Aby mieć dane do kalkulacji / szacowania kosztów i nakładu pracy
- Aby stworzyć bazę wiedzy. Często jest tak że po ustaleniu przyczyn jakiejś nietypowej awarii mówimy sobie: „No tak, ja już taki przypadek kiedyś miałem”
Zgłoszenia awarii
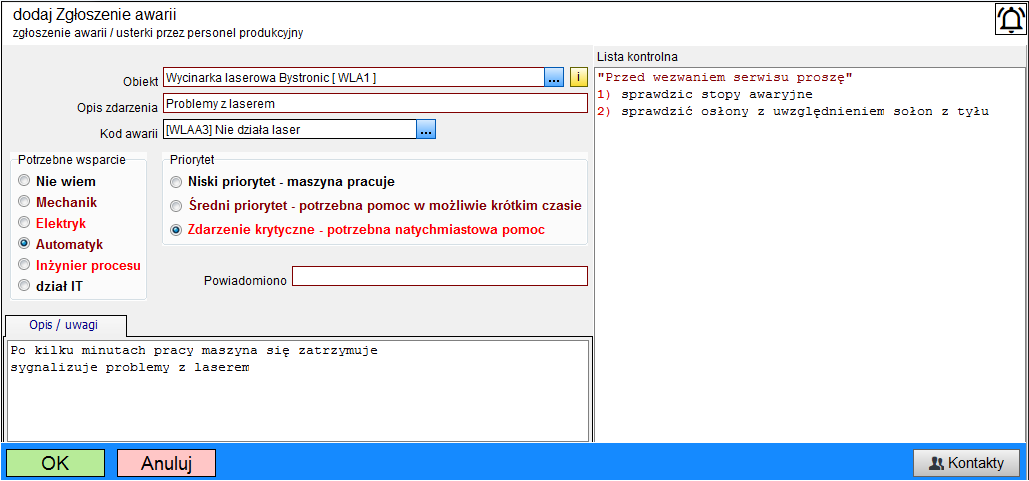
Aby personel UR zareagował na awarie to musi o niej wiedzieć i to jak najszybciej. A z tym bywa różnie. Dlatego pracownicy produkcyjni czy ich bezpośredni przełożeni powinni mieć możliwość wprowadzania informacji o awariach do systemu.
Cele są dwa: pierwszy to przywołanie pomocy. Ale tu trzeba zachować ostrożność. To nie jest tak że na warsztacie siedzi mechanik z elektrykiem, grają w szachy i wyczekują na wezwanie. Nawet jeśli system pozwala na powiadomienia SMS to nie ma gwarancji że pracownik przeczyta wiadomość natychmiast. To jest trudna praca wymagająca uwagi i rozwagi i nikt nie będzie się rozpraszał wiadomościami leżąc pod maszyną. Tak wiec bezpośredniego kontaktu człowiek człowiek nic nie zastąpi. No chyba że jest ktoś kto ma obowiązek przyjmować zgłoszenia i dysponować pracą kolegów.
Drugi cel to rejestracja i upublicznienie zgłoszeń. Dzwoni dziewczyna o pierwszej w nocy i mówi:
„PH2 wszystkie blistry wyrzuca jako braki ale przyjdź za godzinę bo idziemy na kawę”
Tak kiedyś mogło być bo po naszej rozmowie nie zostawał żaden ślad i tylko my o tym wiedzieliśmy. Wprowadzenie zgłoszenia do systemu staje się widoczne dla wielu osób a nader wszystko można sprawdzić że awaria została zgłoszona ok. 11:30 a nie o 10 jak upiera się produkcja.
Wizualizacja
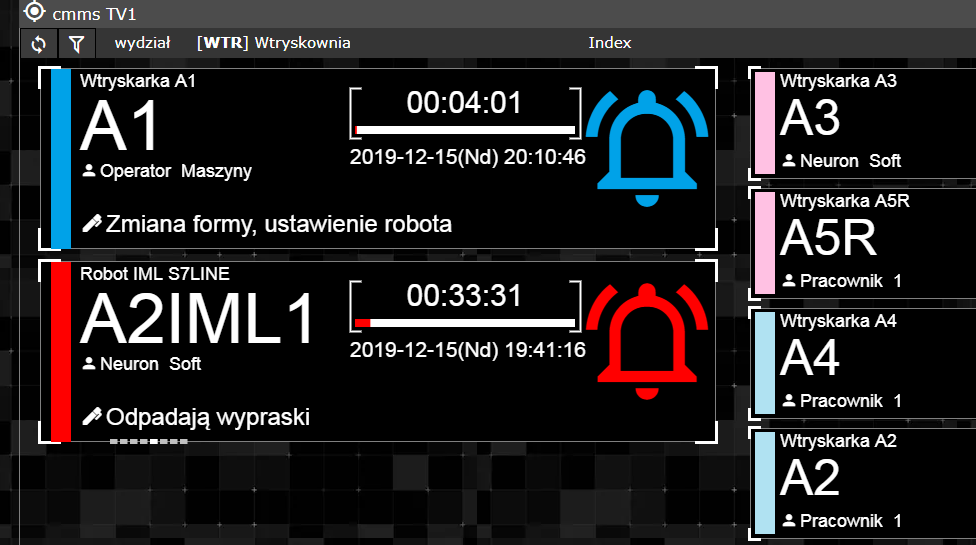
cmms maszyna - serwer aplikacji mobilnych - aplikacja TV
Coraz powszechniejsze stają się wizualizacje z użyciem dużych monitorów czy telewizorów na halach produkcyjnych. Widoczne są nie tylko zgłoszenia które „kłują wszystkich po oczach” ale też awarie czy usterki w toku dzięki czemu produkcja wie że wezwana pomoc spóźnia się nie przez lenistwo pracowników UR a dla tego że pracują przy kilku innych awariach.
Przeglądy prewencyjne (PM)
Przeglądy prewencyjne, zwane też przeglądami okresowymi to trzon utrzymania ruchu a co za tym idzie ważnymi modułami w programach CMMS są wszelkiego rodzaju harmonogramy pozwalające na ich planowanie.Inspekcja, przegląd, konserwacja ?
Wojtek Mączyński z Woma Solutions mawia że konserwować to można ogórki. Ja z kolei zawsze trzymałem się tezy że nadmiar precyzji prowadzi do chaosu. Niemniej wielu terminów związanych z PM używa się zamiennie dlatego spróbujmy je usystematyzować:- Inspekcja to okresowa kontrola stanu technicznego, często z użyciem narzędzi diagnostycznych.
Cechą charakterystyczną jest brak konieczności długotrwałego wyłączenia maszyny z ruchu - Przegląd techniczny to połączenie dogłębnej inspekcji z następczą i/lub planowaną wymianą zużywających się komponentów.
- Remont to „odbudowa” sprawności maszyny poprzez gruntowne i daleko idące działania
- Modyfikacje ( KAIZEN ) to działania mające na celu nie tyle utrzymanie sprawności obiektu co podwyższenie jego funkcjonalności i bezpieczeństwa.
Po co robimy przeglądy
Nie sposób zrozumieć czym jest obsługa prewencyjna bez zrozumienia czym jest zmienność niezawodności w czasie. Każdy produkt ma swój cykl życia podzielony na trzy etapy: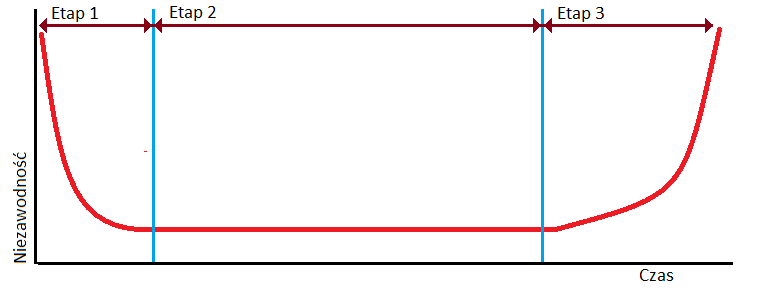
Etap 1 to etap wczesnego dzieciństwa, lub bardziej profesjonalnie, etap wczesnych uszkodzeń. Większe ryzyko awarii na tym etapie wynika z wad fabrycznych, wad materiałów, montażu a w przypadku maszyn, uszkodzeń przy ich relokacji, błędów w projekcie i błędów pracowników którzy dopiero uczą się ich obsługi.
Na tym etapie królują reaktywne działania UR – ciężko planować przeglądy w pierwszych tygodniach działania maszyny, głownie dla tego że dopiero „się jej uczymy”.
Kolejny etap to okres normalnej pracy. Na tym etapie możemy oczekiwać w miarę stałej ilości awarii a działania powinny się koncentrować na maksymalnym wydłużeniu tego czasu.
Inspekcje sprawdzające czy „coś nie cieknie, coś nie wisi, coś nie hałasuje lub się nadmienię grzeje”, pogłębione inspekcje wymagające np. demontażu osłon, regulacje elementów przeniesienia napędu, ustawienia czujników etc. Wymiana zużywających się szybciej niż cała maszyna jej elementów na podstawie obserwacji, pomiarów albo zaleceń producenta. No i szeroko rozumiane smarowanie, wymiana olejów, nadzór nad centralnymi systemami smarowania.
Ostatnim etapem jest okres zużycia. Ilość awarii zaczyna rosnąć z powodu zużycia poszczególnych elementów oraz „zmęczenia materiałów i systemów”. Zwiększenie częstotliwości przeglądów nie daje oczekiwanych efektów a często jedynie zwiększa koszty obsługi.
Możemy jednak w tym momencie rozważyć coś co potocznie nazywa się remontem maszyny, dokonać daleko idących czynności które niejako „zrestartują” nasz wykres.
Harmonogram przeglądów
Harmonogramowaniu przeglądów towarzyszy błędne przekonanie że to łatwe zadanie, że właściwie wystarczy ustalić jakiś interwał, np. co miesiąc i się samo zaplanuje.Aby zaplanować przegląd PM należy
- ustalić zakres prac właściwy dla danego typu przeglądu i czas jego realizacji, w tym podzielić czas na czynności nie wymagające zatrzymania maszyny.
- ustalić termin
- ustalić priorytety na wypadek zbiegu kilku zadań w tym samym czasie.
- uzgodnić termin przeglądu z produkcją
- ustalić termin z producentem / usługodawcą jeśli wymagane jest wsparcie z „zewnątrz”
- być gotowym na zmianę terminu na wniosek produkcji
- być gotowym na zmianę terminu jeśli zewnętrzny usługodawca nie będzie miał „okienka”
- zarezerwować pracownika/pracowników w odpowiednim wymiarze czasu
- zarezerwować części i materiały
- zarezerwować budżet, szczególnie jeśli termin wypada w nowym roku finansowym
- zarezerwować narzędzia diagnostyczne, jeśli nie posiadamy swoich
- jeśli łączymy PM z predykcją uwzględnić modyfikacje terminu, np. wzrost wibracji może wymusić zmiany w harmonogramie
- jeśli wymagają tego wymogi formalne po wykonaniu dokonać odbioru prac
Częstotliwość prac
Przeglądy prewencyjne określa się też jako okresowe bo wykonywane są co jakiś czas. Najbardziej optymalnym wydaje się planowanie w krótkim terminie na podstawie przesłanek z analizy historii i stanu obiektu ale to co najlepsze często najtrudniej zaakceptować.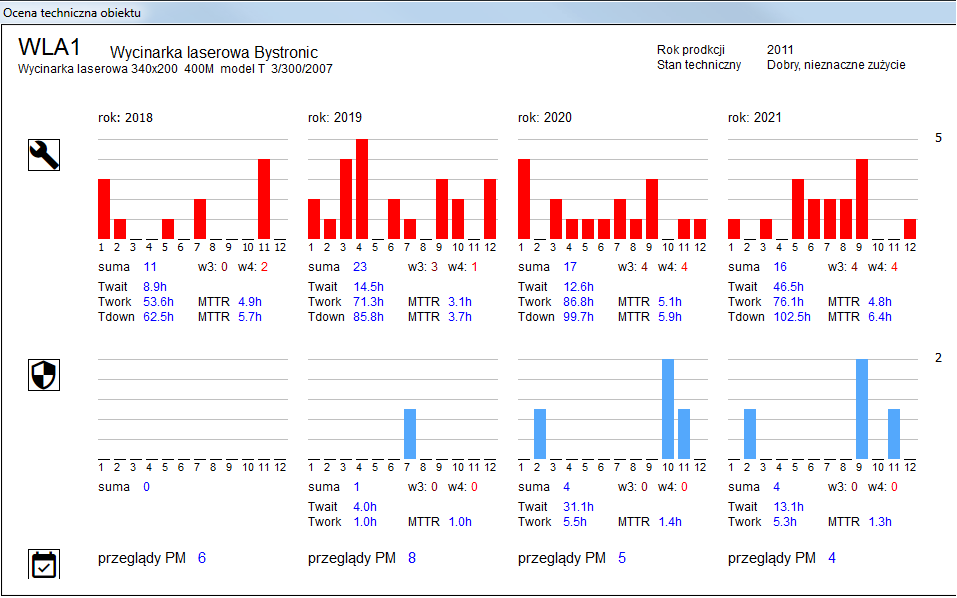
Każdy CMMS ma opcję generowania lub odtwarzania serii przeglądów z różnymi interwałami. Projektujemy przegląd i każemy go powtórzyć co miesiąc, co kwartał itp.
I było by cudownie gdyby nie ta niedobra produkcja która nie chce nam dać dostępu do maszyn. Dziś nie, jutro nie, mamy tyle pracy że najlepiej w tym miesiącu nie ….
Ale w czym problem? Przecież wystarczy się z produkcją umówić, a najlepiej wspólnie z nią planować. Możemy sobie wyobrazić integrację systemów CMMS z systemami harmonogramowania produkcji APS. Tyle ze typowy harmonogram produkcji opiewa na 2 do 4 tygodnie. A nasz harmonogram na rok.
Harmonogram a predykcja
Predykcyjne utrzymanie ruchu, szczególnie oparte o nowoczesne technologie takie jak np. pomiary wibracji z ich analizą przez algorytmy otwiera nowe, niesamowite możliwości. Ale też rodzi pewne problemy o czym zapominamy.Predykcja może być oparta na dwu modelach. Pierwszy to natychmiastowa reakcja na awarię. Zatrzymujemy maszynę aby zminimalizować jej skutki a prognoza ma zasięg minut.
Drugi model to wyznaczanie poziomu ryzyka. System nie powie że awaria będzie w środę o 11:45 tylko że rośnie jej ryzyko, czasami w perspektywie dni a czasami tygodni.
I co wtedy robimy? Wykluczamy maszynę z produkcji na podstawie przesłanek? Nie. Zmieniamy harmonogram PM. Planowaliśmy gruntowny przegląd za 2 miesiące, przesuwany go na pojutrze.
Dużo się mówi o przemyśle 4.0. Niestety na razie mamy przemysł 3.25. Przyszłością nie są jakieś czujniki przyklejone do maszyn, przyszłością są spójne systemy produkcyjne gdzie nie będzie podziału na harmonogram UR czy produkcji, gdzie będzie jeden spójny, dynamiczny, adaptujący się do potrzeb, okoliczności i zakłóceń harmonogram dla całej cyfrowej fabryki.
Gospodarka magazynowa
Stałym elementem gry w systemach CMMS jest zarządzanie częściami zapasowymi i materiałami eksploatacyjnymi. Ktoś powie, gospodarka jak każda inna. Nie do końca, choćby dla tego że w UR każda szafa, każda szuflada czy torba elektryka jest małym magazynem. Część zasobów po przejściu przez procedury zakupowe trafia poza ewidencję. Pytanie czy jest to 3 czy 30%.Zarządzanie zapasami
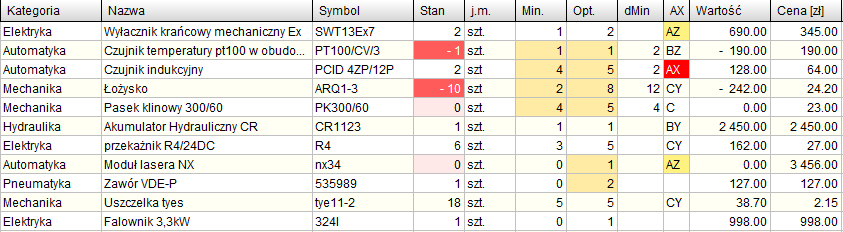
Zasoby utrzymania ruchu mają jedną bardzo nieelegancką cechę – ograniczoną przewidywalność zużycia. Jedna część będzie leżeć na półce 5 lat, innej w roku 5 razy zabraknie. Każda pozycja na magazynie to zamrożone aktywo ale jej brak w momencie awarii to wymierna strata. Czasami niewspółmierna gdy część warta 20zł zablokuje nam maszynę na wiele godzin a nawet dni.
Dlatego moduł magazynowy powinien pozwalać nie tylko na zarządzanie przepływem wartości ale też na analizę ilości posiadanej i pożądanej, na definiowanie stanów minimalnych i optymalnych, na określenie „ważności i dostępności” poszczególnych pozycji, np. za pomocą klasyfikacji ABC XYZ, na określenie zużycia części w różnych kontekstach.
Części pobieramy dla konkretnej pracy
Czy sama wiedza o aktualnej wartości magazynu części zamiennych, o wartości przychodów i rozchodów nam wystarczy? Nie. My chcemy znać koszty w ujęciu konkretnej maszyny, wydziału, z podziałem na obsługę planowaną i doraźną itd.Dlatego części zawsze pobiera się w konkretnym celu. Nie wystarczy na magazynie „piknąć” kolektorem w kod części a system zdejmie nam jedną sztukę. Musimy wiedzieć na jaką operację ta część została pobrana: awaria, przegląd, mała inwestycja a pośrednio w koszt jakiej maszyny i jakiego działu została zużyta.
I nie chodzi tu o przypisanie do rozchodu jakiejś kategorii typu awaria, eksploatacja czy innej, chodzi o przypisanie tej konkretnej części do tej konkretnej pracy. A że praca przypisana jest do konkretnego obiektu to i zużyta część jest do niego przypisana.
Analiza zużycia części przez konkretną maszynę ma też wartość diagnostyczną. Wymieniając jakiś element nie zawsze mamy świadomość ze robimy to już czwarty raz w tym roku i należy się zastanowić co jest tego przyczyną.
Podwójna gospodarka magazynowa
Największym problemem jest podwójny obieg dokumentów. Tylko nieliczne firmy mają gospodarkę magazynową UR odrębna od gospodarki magazynowej firmy, czasami z własną księgowością. W większości firm część która jest na stanie w programie CMMS jest też na stanie w innym systemie lub musiała przez inny system przejść.Posłużę się przykładem z czasów gdy pracowałem zawodowo w UR. Potrzebowałem jeden czujnik który wymagał pilnej wymiany w maszynie. Mój szef zamawiał w zaopatrzeniu 10szt. Dlaczego 10? Żeby dostać 5. W końcu zaopatrzenie wie lepiej.
Te 5 sztuk „wchodziło” na magazyn techniczny firmy. Jednym dokumentem. Mój szef pobierał 5 sztuk z magazynu. Też jednym dokumentem.
Ja dostałem 2 sztuki – jedna do maszyny a druga do naszej szafy warsztatowej a 3 sztuki lądowały w szafie mojego szefa.
Były wiec trzy magazyny: magazyn techniczny, najczęściej ze stanami zerowymi, magazyn u szefa i magazyn w naszym warsztacie. W konsekwencji każda część stawała się dla firmy kosztem w dniu zakupu a nie w dniu zużycia a 4 czujniki znalazły się poza ewidencją.
Dlatego prawdopodobnie będziemy potrzebowali DOBRZE poprowadzonej integracji systemu CMMS z systemem ERP/WMS by zapewnić synchronizację stanów magazynowych w dwu odrębnych systemach. Jest to zadanie trudne, kosztowne a efekty często są co najmniej mało satysfakcjonujące.
Raporty
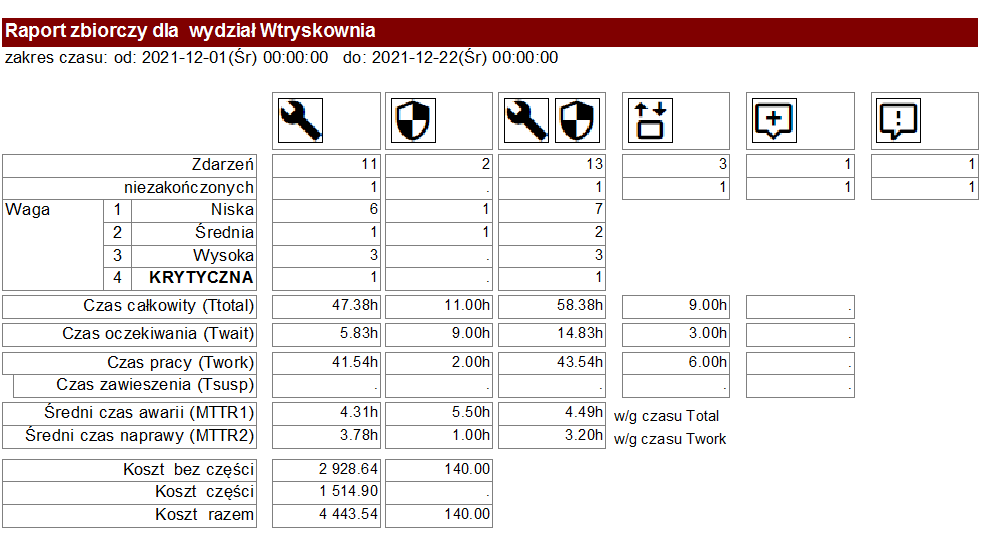
cmms maszyna - fragment raportu zbioczego dla wydziału
Praktycznie każdy moduł a swój zestaw raportów, np. moduł magazynu pozwala na spisy z natury, analizy ilościowe i koszowe a nader wszystko zestawienia rozchodów części na poszczególne maszyny, ich grupy, wydziały produkcyjne. Z kolei z obsługą prewencyjną i reakcyjną skojarzone są takie raporty jak zestawienia czasu pracy i kosztów z podziałem na maszyny i ich grupy ale też na rodzaje prac, zdarzeń, przyczyny awarii. Są też całe moduły raportowe pozwalające np. na obserwację zmienności w czasie, np. zestawienia roczne z podziałem na miesiące.
Musimy jednak mieć na uwadze że jakość generowanych raportów zależy od wiarygodności i spójności dostępnych danych. I nie chodzi tylko o to że mechanik zamiast 37 minut wpisał 30 a czas od awarii liczony jest nie od utraty dostępności maszyny tylko od momentu gdy ktoś to zauważył i zgłosił.
Chodzi o to że często system CMMS jeśli nie współpracuje z systemem MES nie dysponuje wieloma informacjami. Wiemy że w miesiącu było 14 godzin awarii ale przyjmujemy często że miesiąc ma 744 godziny i zakładamy że tyle czasu maszyna pracowała. A postoje planowane, np. brak zleceń czy wolne dni? A postoje nieplanowane z innych przyczyn niż awarie? Więc jaki procent czasu pracy maszyny stanowią awarie?
Wskaźniki KPI dla UR
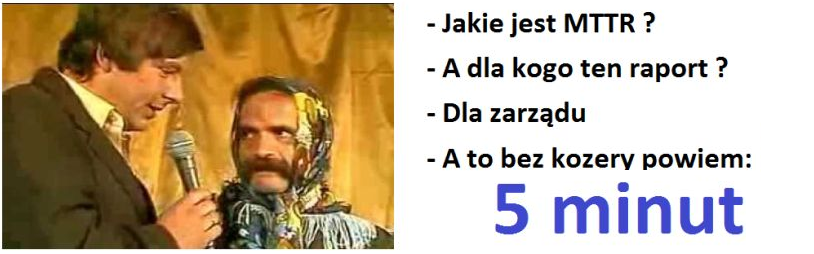
Wskaźniki MTTR i MTBF są bardzo pożytecznymi narzędziami do szybkiej WSTĘPNEJ oceny niezawodności maszyny i skuteczności działań na niej. Niestety panuje ułudna wiara że ich zmienność w czasie może być bezkrytycznie użyta do badania efektywności pracy UR.
Weźmy MTTR. Czas awarii podzielony przez ich ilość. Ale czas czego? Niedostępności maszyny? Naprawy? Pracy przy naprawie? To nie jest to samo. Prosta sytuacja: wózek widłowy wjechał w transporter maszyny, po dwu tygodniach serwis producenta zainstalował nowy.
Czas niedostępności 366 godzin. Powiedzmy że w miesiącu były jeszcze 4 awarie tej maszyny po 2 godziny więc średni czas awarii: MTTR= 374/5 = 74,8 godzin.
Co tak wysoka średnia mówi o niezawodności maszyny? Nic, maszyna się nie zepsuła, ona została zepsuta. Co mówi o pracy techników? Nic, przy najdłuższej awarii pracowali dosłownie kilkanaście minut.
Jeśli nie znamy kontekstu to wskaźniki mogą nas wprowadzić w błąd. A przecież my nie chcemy znać kontekstu, nie mamy na to czasu. Mało tego, my nie chcemy znać wskaźników dla maszyn, my chcemy, my ŻĄDAMY jednego wskaźnika dla całej fabryki.
O tym jak skomplikowanymi wskaźnikami są MTTR i MTBF przeczytasz w naszym artykule: MTBF MTTR w praktyce
TPM
TPM ( total productive maintenance ) ma wiele znaczeń ale możemy założyć że to częściowe przeniesienie zadań UR na pracowników produkcyjnych. Działań polegających na codziennych przeglądach stanu maszyn, na ich konserwacji, wstępnej diagnostyce przed wezwaniem pomocy. Działań które mają odciążyć pracowników działu UR cierpiących często na chroniczny brak czasu.Nie można jednak pracownikom po prostu powiedzieć „macie zrobić” tylko trzeba stworzyć dla nich dobrze przemyślane procedury postępowania i stworzyć sensowny sposób nadzoru nad ich pracą w tym zakresie.
Dlatego systemy CMMS implementują szereg narzędzi dla wsparcia autonomicznego utrzymania ruchu ( Autonomous Maintenance ) takich jak karty kontrolne, wnioski kaizen etc.
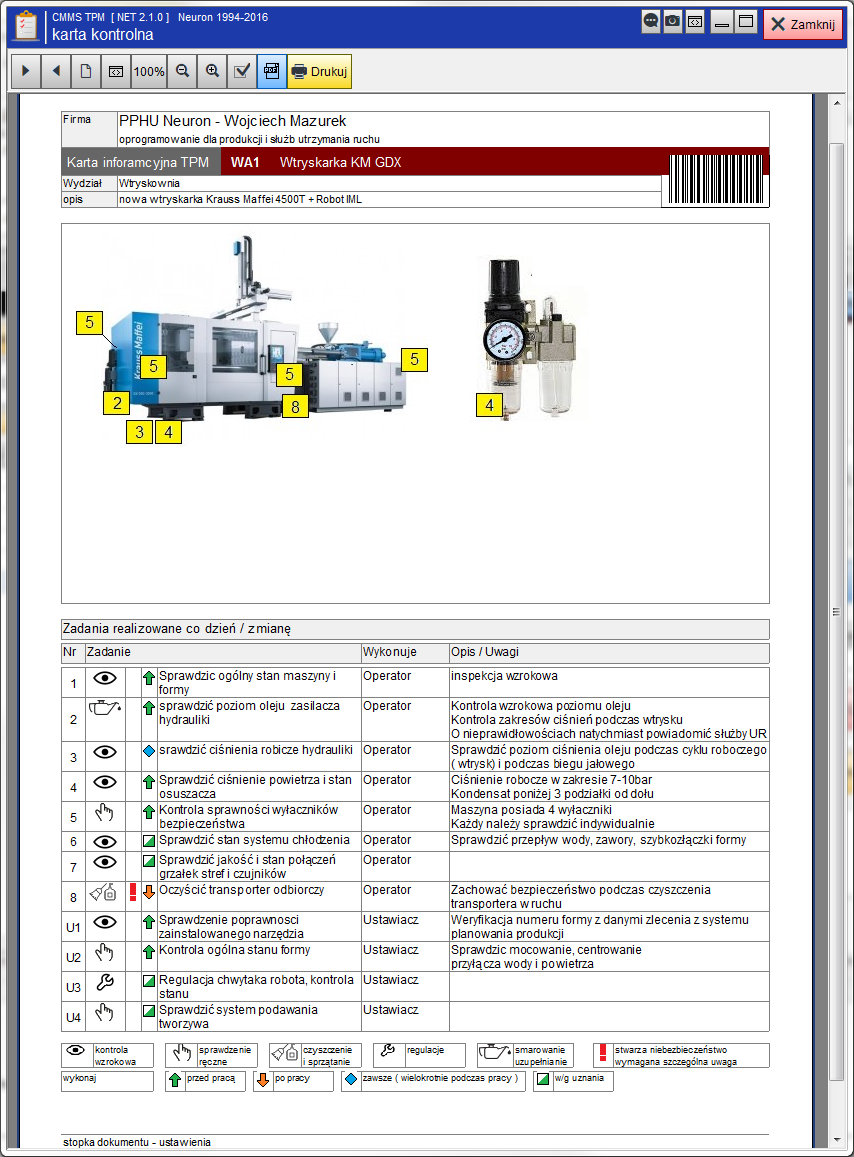
program CMMS TPM - przykład karty kontrolnej
TPM w praktyce
CMMS w małej firmie
„Oprogramowanie CMMS to jest proszę Pana dla dużych firm. Ja mam 10 maszyn. Ja wszystko wiem a jak się coś zepsuje to mam taki zeszyt a w nim kilka numerów telefonów.”No i się zepsuło. Przybywa pomoc:
- ktoś tu coś robił?
- nie, nie wiem, chyba 2 lata temu, nie pamiętam.
- a jakieś części do tego macie?
- no coś tam dali jak kupowałem ale gdzie to jest nie wiem.
- a schematy?
- a w szafie sterującej nie ma?
Jeszcze ciekawiej może być jak małą firmę odwiedzi inspektor PiP i poprosi o dokumenty, np. deklarację CE. Albo zakwestionuje brak osłony a my nie wiemy gdzie jest DTR’ka aby udowodnić że takowej nigdy nie było.
Nawet w małym warsztacie czy niewielkim markecie jest tyle technicznego dobra wymagającego obsługi technicznej i formalnej że warto pomyśleć o czymś więcej niż notes czy arkusz.
Podsumowanie
Jak widać temat systemów CMMS, a szerzej temat utrzymania ruchu to temat rzeka. Nie dotknąłem nawet połowy zagadnień, nie mówiąc o ich rozwinięciu.Na koniec powiem tak: w utrzymaniu ruchu NIC NIGDY nie jest tak proste jak się może wydawać. Zakup oprogramowania, czy to taniego i prostego czy drogiego skomplikowanego systemu z dużą pulą godzin pracy wdrożeniowców jest dopiero początkiem długiej i szalenie krętej drogi.